Als kritischer Schritt im Halbleiterherstellungsprozess ist die Wafer-Dicing-Technologie direkt mit der Chipleistung, dem Ertrag und den Produktionskosten verknüpft.
#01 Hintergrund und Bedeutung des Wafer-Dicing
1.1 Definition des Wafer-Dicing
Das Wafer-Dicing (auch bekannt als Ritzen) ist ein wesentlicher Schritt in der Halbleiterfertigung. Ziel ist es, bearbeitete Wafer in mehrere einzelne Chips zu zerlegen. Diese Chips enthalten typischerweise die komplette Schaltungsfunktionalität und sind die Kernkomponenten, die letztendlich bei der Herstellung elektronischer Geräte zum Einsatz kommen. Da Chipdesigns immer komplexer und die Abmessungen immer kleiner werden, steigen die Anforderungen an Präzision und Effizienz der Wafer-Dicing-Technologie.
In der Praxis werden beim Wafer-Dicing typischerweise hochpräzise Werkzeuge wie Diamantklingen eingesetzt, um sicherzustellen, dass jeder Chip intakt und voll funktionsfähig bleibt. Wichtige Schritte sind die Vorbereitung vor dem Schneiden, die präzise Kontrolle während des Schneidvorgangs und die Qualitätskontrolle nach dem Schneiden.
Vor dem Schneiden muss der Wafer markiert und positioniert werden, um präzise Schneidepfade zu gewährleisten. Während des Schneidens müssen Parameter wie Werkzeugdruck und -geschwindigkeit streng kontrolliert werden, um eine Beschädigung des Wafers zu vermeiden. Nach dem Schneiden werden umfassende Qualitätsprüfungen durchgeführt, um sicherzustellen, dass jeder Chip die Leistungsstandards erfüllt.
Die grundlegenden Prinzipien der Wafer-Dicing-Technologie umfassen nicht nur die Auswahl der Schneideausrüstung und die Einstellung der Prozessparameter, sondern auch den Einfluss der mechanischen Eigenschaften und Materialmerkmale auf die Schnittqualität. Beispielsweise sind Low-k-dielektrische Siliziumwafer aufgrund ihrer schlechteren mechanischen Eigenschaften sehr anfällig für Spannungskonzentrationen beim Schneiden, was zu Fehlern wie Absplitterungen und Rissen führt. Die geringe Härte und Sprödigkeit von Low-k-Materialien machen sie anfälliger für Strukturschäden unter mechanischer oder thermischer Belastung, insbesondere beim Schneiden. Der Kontakt zwischen Werkzeug und Waferoberfläche in Verbindung mit hohen Temperaturen kann die Spannungskonzentration zusätzlich verstärken.
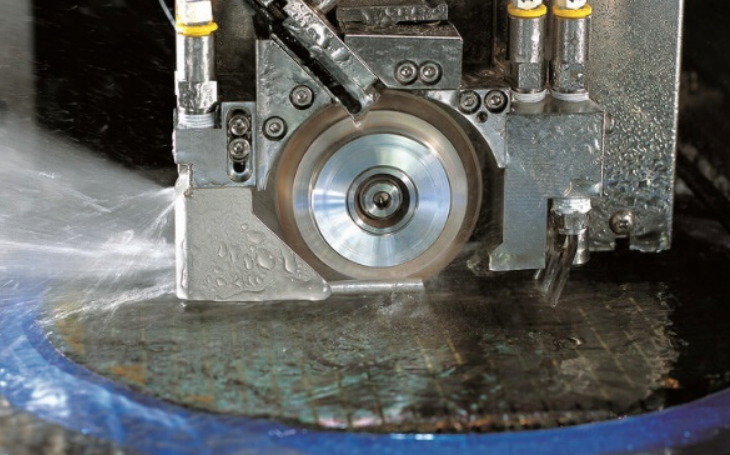
Dank der Fortschritte in der Materialwissenschaft hat sich die Wafer-Dicing-Technologie über traditionelle Silizium-Halbleiter hinaus erweitert und umfasst nun auch neue Materialien wie Galliumnitrid (GaN). Diese neuen Materialien stellen aufgrund ihrer Härte und strukturellen Eigenschaften neue Herausforderungen für Dicing-Prozesse dar und erfordern weitere Verbesserungen bei Schneidwerkzeugen und -techniken.
Als kritischer Prozess in der Halbleiterindustrie wird das Wafer-Dicing kontinuierlich optimiert, um den sich entwickelnden Anforderungen und technologischen Fortschritten gerecht zu werden und so den Grundstein für zukünftige Mikroelektronik- und integrierte Schaltkreistechnologien zu legen.
Verbesserungen in der Wafer-Dicing-Technologie gehen über die Entwicklung von Hilfsmaterialien und Werkzeugen hinaus. Sie umfassen auch Prozessoptimierungen, Leistungssteigerungen der Geräte und eine präzise Steuerung der Dicing-Parameter. Diese Fortschritte zielen darauf ab, hohe Präzision, Effizienz und Stabilität im Wafer-Dicing-Prozess zu gewährleisten und so dem Bedarf der Halbleiterindustrie nach kleineren Abmessungen, höherer Integration und komplexeren Chipstrukturen gerecht zu werden.
Verbesserungsbereich | Spezifische Maßnahmen | Auswirkungen |
Prozessoptimierung | - Verbessern Sie die anfänglichen Vorbereitungen, beispielsweise durch eine genauere Waferpositionierung und Pfadplanung. | - Reduzieren Sie Schnittfehler und verbessern Sie die Stabilität. |
- Minimieren Sie Schnittfehler und verbessern Sie die Stabilität. | - Nutzen Sie Echtzeitüberwachungs- und Feedbackmechanismen, um Werkzeugdruck, Geschwindigkeit und Temperatur anzupassen. | |
- Geringere Waferbruchraten und verbesserte Chipqualität. | ||
Leistungssteigerung der Ausrüstung | - Nutzen Sie hochpräzise mechanische Systeme und fortschrittliche Automatisierungssteuerungstechnologie. | - Verbessern Sie die Schnittgenauigkeit und reduzieren Sie Materialverschwendung. |
- Einführung einer Laserschneidtechnologie, die für Wafer aus Materialien mit hoher Härte geeignet ist. | - Verbessern Sie die Produktionseffizienz und reduzieren Sie manuelle Fehler. | |
- Erhöhen Sie die Geräteautomatisierung für automatische Überwachung und Anpassungen. | ||
Präzise Parametersteuerung | - Passen Sie Parameter wie Schnitttiefe, Geschwindigkeit, Werkzeugtyp und Kühlmethoden genau an. | - Gewährleisten Sie die Chipintegrität und elektrische Leistung. |
- Passen Sie die Parameter basierend auf Wafermaterial, -dicke und -struktur an. | - Steigern Sie die Ausbeute, reduzieren Sie Materialabfälle und senken Sie die Produktionskosten. | |
Strategische Bedeutung | - Erkunden Sie kontinuierlich neue technologische Wege, optimieren Sie Prozesse und verbessern Sie die Gerätekapazitäten, um den Marktanforderungen gerecht zu werden. | - Verbessern Sie Ertrag und Leistung bei der Chipherstellung und unterstützen Sie die Entwicklung neuer Materialien und fortschrittlicher Chipdesigns. |
1.2 Die Bedeutung des Wafer-Dicing
Das Wafer-Dicing spielt eine entscheidende Rolle im Halbleiterherstellungsprozess und hat direkten Einfluss auf nachfolgende Schritte sowie auf die Qualität und Leistung des Endprodukts. Seine Bedeutung lässt sich wie folgt beschreiben:
Erstens sind Genauigkeit und Konsistenz beim Dicing entscheidend für Chipausbeute und Zuverlässigkeit. Während der Herstellung durchlaufen Wafer mehrere Verarbeitungsschritte, um zahlreiche komplexe Schaltungsstrukturen zu bilden, die präzise in einzelne Chips (Dies) zerlegt werden müssen. Treten beim Dicing erhebliche Fehler bei der Ausrichtung oder beim Schneiden auf, können die Schaltungen beschädigt werden, was die Funktionalität und Zuverlässigkeit des Chips beeinträchtigt. Daher gewährleistet hochpräzise Dicing-Technologie nicht nur die Integrität jedes Chips, sondern verhindert auch Schäden an internen Schaltungen und verbessert so die Gesamtausbeute.
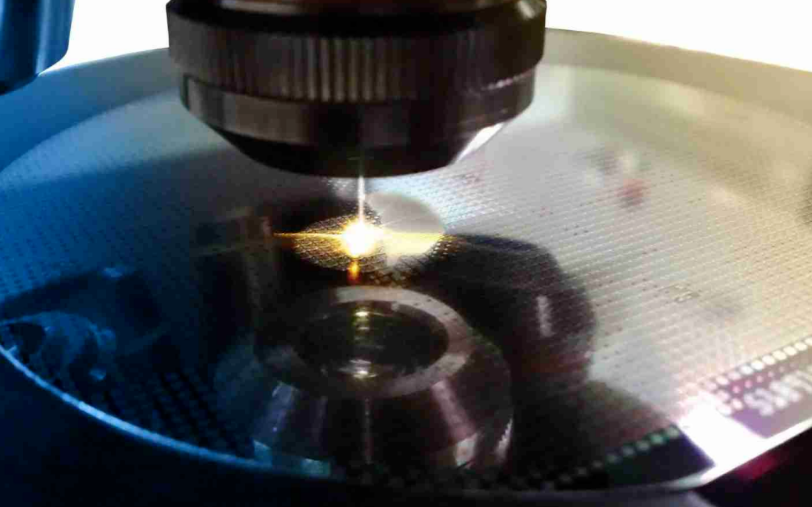
Zweitens hat das Wafer-Dicing einen erheblichen Einfluss auf die Produktionseffizienz und die Kostenkontrolle. Als entscheidender Schritt im Herstellungsprozess beeinflusst seine Effizienz direkt den Fortschritt nachfolgender Schritte. Durch die Optimierung des Dicing-Prozesses, die Erhöhung des Automatisierungsgrades und die Verbesserung der Schneidegeschwindigkeit kann die Gesamtproduktionseffizienz deutlich gesteigert werden.
Andererseits ist der Materialverlust beim Dicing ein kritischer Faktor im Kostenmanagement. Der Einsatz moderner Dicing-Technologien reduziert nicht nur unnötige Materialverluste beim Schneideprozess, sondern erhöht auch die Waferauslastung und senkt so die Produktionskosten.
Mit dem Fortschritt in der Halbleitertechnologie nehmen die Waferdurchmesser stetig zu und damit auch die Schaltungsdichte. Dies stellt höhere Anforderungen an die Dicing-Technologie. Größere Wafer erfordern eine präzisere Steuerung der Schneidewege, insbesondere in Bereichen mit hoher Schaltungsdichte, wo selbst kleinste Abweichungen zu Defekten in mehreren Chips führen können. Zudem erfordern größere Wafer mehr Schneidelinien und komplexere Prozessschritte. Um diesen Herausforderungen gerecht zu werden, sind weitere Verbesserungen der Präzision, Konsistenz und Effizienz der Dicing-Technologien erforderlich.
1.3 Wafer-Dicing-Prozess
Der Wafer-Dicing-Prozess umfasst alle Schritte von der Vorbereitungsphase bis zur abschließenden Qualitätskontrolle. Jeder Schritt ist entscheidend für die Qualität und Leistung der gesägten Chips. Nachfolgend finden Sie eine detaillierte Erläuterung der einzelnen Phasen.
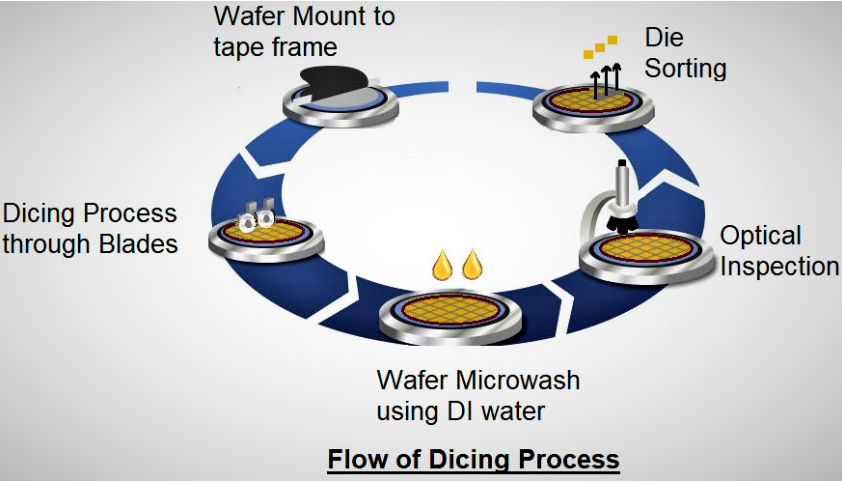
Phase | Detaillierte Beschreibung |
Vorbereitungsphase | -Waferreinigung: Verwenden Sie hochreines Wasser und spezielle Reinigungsmittel in Kombination mit Ultraschall- oder mechanischem Schrubben, um Verunreinigungen, Partikel und Schadstoffe zu entfernen und eine saubere Oberfläche zu gewährleisten. -Präzise Positionierung: Verwenden Sie hochpräzise Geräte, um sicherzustellen, dass der Wafer entlang der vorgesehenen Schnittpfade präzise geteilt wird. -Waferfixierung: Befestigen Sie den Wafer auf einem Bandrahmen, um die Stabilität während des Schneidens aufrechtzuerhalten und Schäden durch Vibrationen oder Bewegungen zu vermeiden. |
Schneidphase | -Klingenwürfeln: Verwenden Sie zum physikalischen Schneiden schnell rotierende, diamantbeschichtete Klingen, die für siliziumbasierte Materialien geeignet und kostengünstig sind. -Laser-Dicing: Nutzen Sie hochenergetische Laserstrahlen zum berührungslosen Schneiden, ideal für spröde oder hochharte Materialien wie Galliumnitrid, und bieten Sie höhere Präzision und weniger Materialverlust. -Neue Technologien: Einführung von Laser- und Plasmaschneidtechnologien zur weiteren Verbesserung von Effizienz und Präzision bei gleichzeitiger Minimierung der Wärmeeinflusszonen. |
Reinigungsphase | - Verwenden Sie deionisiertes Wasser (DI-Wasser) und spezielle Reinigungsmittel in Kombination mit Ultraschall- oder Sprühreinigung, um beim Schneiden entstehende Rückstände und Staub zu entfernen und zu verhindern, dass Rückstände nachfolgende Prozesse oder die elektrische Leistung des Chips beeinträchtigen. - Hochreines deionisiertes Wasser verhindert die Einführung neuer Verunreinigungen und gewährleistet eine saubere Waferumgebung. |
Inspektionsphase | -Optische Inspektion: Verwenden Sie optische Erkennungssysteme in Kombination mit KI-Algorithmen, um Defekte schnell zu identifizieren und sicherzustellen, dass die gewürfelten Chips keine Risse oder Absplitterungen aufweisen. Dadurch wird die Inspektionseffizienz verbessert und menschliches Versagen reduziert. -Dimensionsmessung: Überprüfen Sie, ob die Chipabmessungen den Designspezifikationen entsprechen. -Elektrische Leistungsprüfung: Stellen Sie sicher, dass die elektrische Leistung kritischer Chips den Standards entspricht, und garantieren Sie so die Zuverlässigkeit in nachfolgenden Anwendungen. |
Sortierphase | - Verwenden Sie Roboterarme oder Vakuumsauger, um qualifizierte Chips vom Bandrahmen zu trennen und sie automatisch nach Leistung zu sortieren. So gewährleisten Sie Produktionseffizienz und Flexibilität bei gleichzeitiger Verbesserung der Präzision. |
Der Waferschneideprozess umfasst die Reinigung, Positionierung, das Schneiden, Reinigen, Prüfen und Sortieren der Wafer, wobei jeder Schritt entscheidend ist. Dank Fortschritten in der Automatisierung, im Laserschneiden und in KI-Inspektionstechnologien erreichen moderne Waferschneidesysteme höhere Präzision, Geschwindigkeit und geringeren Materialverlust. Neue Schneidtechnologien wie Laser und Plasma werden künftig das traditionelle Klingenschneiden schrittweise ersetzen, um den Anforderungen immer komplexerer Chipdesigns gerecht zu werden und die Entwicklung der Halbleiterfertigung weiter voranzutreiben.
Waferschneidtechnologie und ihre Prinzipien
Das Bild veranschaulicht drei gängige Waferschneidetechnologien:Klingenwürfeln,Laser-Dicing, UndPlasma-DicingNachfolgend finden Sie eine detaillierte Analyse und ergänzende Erläuterung dieser drei Techniken:
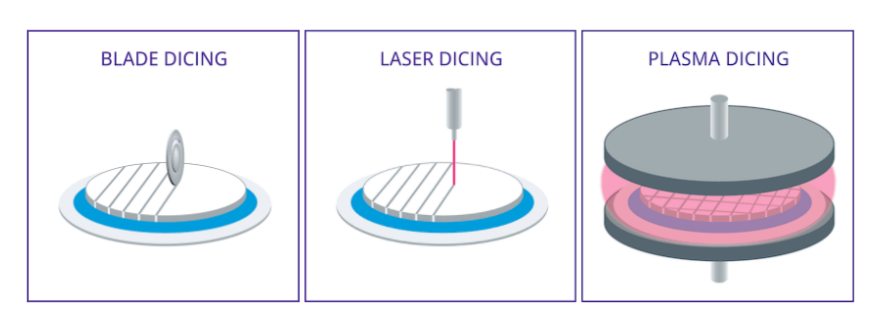
In der Halbleiterfertigung ist das Waferschneiden ein entscheidender Schritt. Dabei muss das geeignete Schneidverfahren basierend auf der Waferdicke ausgewählt werden. Der erste Schritt besteht darin, die Waferdicke zu bestimmen. Übersteigt die Waferdicke 100 Mikrometer, kann das Blade-Dicing als Schneidverfahren gewählt werden. Ist Blade-Dicing nicht geeignet, kann das Fraktur-Dicing-Verfahren eingesetzt werden, das sowohl Ritz- als auch Blade-Dicing-Techniken umfasst.
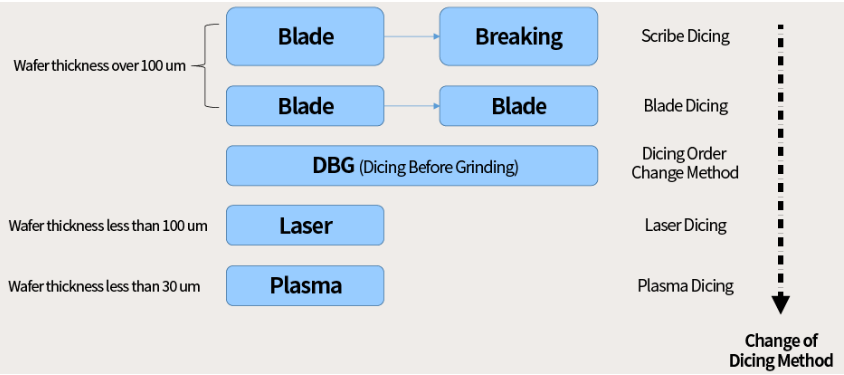
Bei Waferdicken zwischen 30 und 100 Mikrometern empfiehlt sich die DBG-Methode (Dice Before Grinding). In diesem Fall können Ritzschnitt, Blade-Dicing oder eine bedarfsgerechte Anpassung der Schnittreihenfolge gewählt werden, um optimale Ergebnisse zu erzielen.
Für ultradünne Wafer mit einer Dicke von weniger als 30 Mikrometern ist Laserschneiden die bevorzugte Methode, da es dünne Wafer präzise und ohne übermäßige Beschädigung schneidet. Wenn Laserschneiden bestimmte Anforderungen nicht erfüllt, kann Plasmaschneiden als Alternative eingesetzt werden. Dieses Flussdiagramm bietet einen klaren Entscheidungspfad, um sicherzustellen, dass die am besten geeignete Waferschneidtechnologie für unterschiedliche Dickenbedingungen gewählt wird.
2.1 Mechanische Schneidtechnik
Mechanische Schneidetechnologie ist die traditionelle Methode zum Wafer-Dicing. Das Kernprinzip besteht darin, eine schnell rotierende Diamantschleifscheibe als Schneidwerkzeug zum Schneiden des Wafers zu verwenden. Zu den wichtigsten Komponenten gehört eine luftgelagerte Spindel, die die Diamantschleifscheibe mit hoher Geschwindigkeit antreibt und so präzise Schnitte oder Rillen entlang einer vordefinierten Schnittbahn erzeugt. Diese Technologie ist aufgrund ihrer geringen Kosten, hohen Effizienz und breiten Anwendbarkeit in der Industrie weit verbreitet.
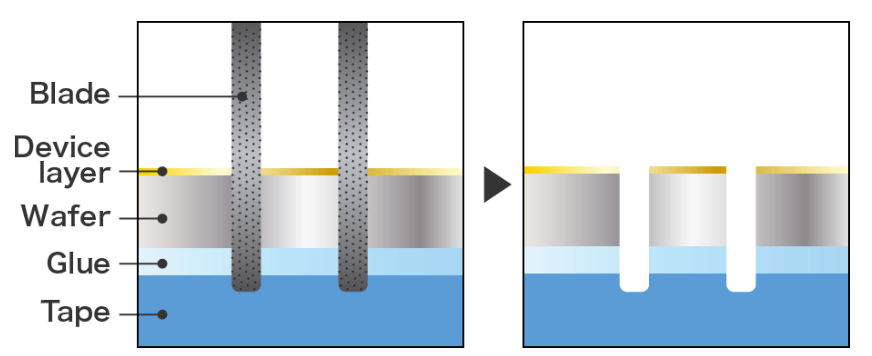
Vorteile
Die hohe Härte und Verschleißfestigkeit von Diamantschleifscheiben ermöglicht die Anpassung der mechanischen Schneidtechnologie an die Schneidanforderungen verschiedener Wafermaterialien, ob traditionelle Silizium-basierte Materialien oder neuere Verbindungshalbleiter. Die Bedienung ist einfach und erfordert relativ geringe technische Anforderungen, was ihre Beliebtheit in der Massenproduktion weiter fördert. Zudem sind die Kosten des mechanischen Schneidens im Vergleich zu anderen Schneidverfahren wie dem Laserschneiden besser kontrollierbar und eignen sich daher für die Massenproduktion.
Einschränkungen
Trotz ihrer zahlreichen Vorteile weist die mechanische Schneidtechnologie auch Einschränkungen auf. Erstens ist die Schneidpräzision aufgrund des physischen Kontakts zwischen Werkzeug und Wafer relativ begrenzt, was häufig zu Maßabweichungen führt, die die Genauigkeit der nachfolgenden Chip-Verpackung und -Prüfung beeinträchtigen können. Zweitens können beim mechanischen Schneidprozess leicht Defekte wie Absplitterungen und Risse auftreten, die nicht nur die Ausbeute beeinträchtigen, sondern auch die Zuverlässigkeit und Lebensdauer der Chips negativ beeinflussen können. Die durch mechanische Belastung verursachten Schäden sind besonders nachteilig für die Herstellung hochdichter Chips, insbesondere beim Schneiden spröder Materialien, bei denen diese Probleme stärker ausgeprägt sind.
Technologische Verbesserungen
Um diese Einschränkungen zu überwinden, optimieren Forscher kontinuierlich den mechanischen Schneidprozess. Zu den wichtigsten Verbesserungen zählen die Verbesserung von Design und Materialauswahl der Schleifscheiben zur Verbesserung von Schnittpräzision und Haltbarkeit. Darüber hinaus hat die Optimierung der Struktur und Steuerungssysteme der Schneideanlagen die Stabilität und Automatisierung des Schneidprozesses weiter verbessert. Diese Fortschritte reduzieren menschliche Fehler und verbessern die Konsistenz der Schnitte. Die Einführung fortschrittlicher Inspektions- und Qualitätskontrolltechnologien zur Echtzeitüberwachung von Anomalien während des Schneidprozesses hat die Schneidzuverlässigkeit und den Schneidertrag ebenfalls deutlich verbessert.
Zukünftige Entwicklung und neue Technologien
Obwohl die mechanische Schneidtechnologie beim Waferschneiden nach wie vor eine bedeutende Rolle spielt, entwickeln sich mit der Weiterentwicklung der Halbleiterprozesse neue Schneidtechnologien rasant weiter. Beispielsweise bietet die Anwendung der thermischen Laserschneidtechnologie neue Lösungen für die Präzisions- und Defektprobleme beim mechanischen Schneiden. Dieses berührungslose Schneidverfahren reduziert die physikalische Belastung des Wafers und verringert das Risiko von Absplitterungen und Rissen deutlich, insbesondere beim Schneiden spröderer Materialien. Die Integration der mechanischen Schneidtechnologie in neue Schneidtechniken wird der Halbleiterfertigung künftig mehr Optionen und Flexibilität bieten und so die Fertigungseffizienz und Chipqualität weiter verbessern.
Zusammenfassend lässt sich sagen, dass die mechanische Schneidetechnologie zwar gewisse Nachteile hat, aufgrund kontinuierlicher technologischer Verbesserungen und ihrer Integration in neue Schneidetechniken jedoch weiterhin eine wichtige Rolle in der Halbleiterherstellung spielen und ihre Wettbewerbsfähigkeit in zukünftigen Prozessen aufrechterhalten wird.
2.2 Laserschneidtechnologie
Die Laserschneidtechnologie als neues Verfahren zum Schneiden von Wafern erfreut sich in der Halbleiterindustrie zunehmender Beliebtheit. Sie zeichnet sich durch hohe Präzision, geringe mechanische Kontaktschäden und schnelle Schneideleistung aus. Diese Technologie nutzt die hohe Energiedichte und Fokussierbarkeit eines Laserstrahls, um eine kleine Wärmeeinflusszone auf der Oberfläche des Wafermaterials zu erzeugen. Trifft der Laserstrahl auf den Wafer, führt die entstehende thermische Spannung zum Bruch des Materials an der gewünschten Stelle und ermöglicht so einen präzisen Schnitt.
Vorteile der Laserschneidtechnologie
• Hohe Präzision: Die präzise Positionierungsfähigkeit des Laserstrahls ermöglicht Schnittpräzisionen im Mikrometer- oder sogar Nanometerbereich und erfüllt damit die Anforderungen der modernen Herstellung hochpräziser integrierter Schaltkreise mit hoher Dichte.
• Kein mechanischer Kontakt: Beim Laserschneiden wird der physische Kontakt mit dem Wafer vermieden, wodurch häufige Probleme beim mechanischen Schneiden, wie Absplittern und Risse, vermieden werden und die Ausbeute und Zuverlässigkeit der Chips deutlich verbessert werden.
• Schnelle Schnittgeschwindigkeit: Die hohe Geschwindigkeit des Laserschneidens trägt zu einer höheren Produktionseffizienz bei und eignet sich daher besonders für groß angelegte Hochgeschwindigkeitsproduktionsszenarien.
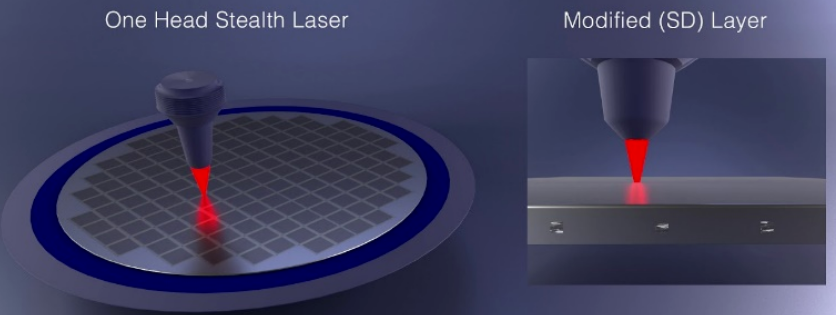
Herausforderungen
• Hohe Gerätekosten: Die Anfangsinvestition für Laserschneidanlagen ist hoch, was insbesondere für kleine und mittlere Produktionsunternehmen einen wirtschaftlichen Druck darstellt.
• Komplexe Prozesssteuerung: Das Laserschneiden erfordert eine präzise Kontrolle mehrerer Parameter, einschließlich Energiedichte, Fokusposition und Schnittgeschwindigkeit, was den Prozess komplex macht.
• Probleme mit der Wärmeeinflusszone: Obwohl die berührungslose Natur des Laserschneidens mechanische Schäden reduziert, kann die thermische Belastung durch die Wärmeeinflusszone (WEZ) die Eigenschaften des Wafermaterials negativ beeinflussen. Um diesen Effekt zu minimieren, ist eine weitere Prozessoptimierung erforderlich.
Richtungen der technologischen Verbesserung
Um diese Herausforderungen zu bewältigen, konzentrieren sich die Forscher auf die Senkung der Gerätekosten, die Verbesserung der Schneideffizienz und die Optimierung des Prozessablaufs.
• Effiziente Laser und optische Systeme: Durch die Entwicklung effizienterer Laser und fortschrittlicher optischer Systeme können die Gerätekosten gesenkt und gleichzeitig die Schnittpräzision und -geschwindigkeit verbessert werden.
• Optimierung der Prozessparameter: Es werden eingehende Untersuchungen zur Wechselwirkung zwischen Lasern und Wafermaterialien durchgeführt, um Prozesse zu verbessern, die die Wärmeeinflusszone reduzieren und dadurch die Schnittqualität verbessern.
• Intelligente Steuerungssysteme: Die Entwicklung intelligenter Steuerungstechnologien zielt darauf ab, den Laserschneidprozess zu automatisieren und zu optimieren und so seine Stabilität und Konsistenz zu verbessern.
Die Laserschneidtechnologie ist besonders effektiv bei ultradünnen Wafern und hochpräzisen Schneidszenarien. Mit zunehmender Wafergröße und steigender Schaltungsdichte können herkömmliche mechanische Schneidverfahren die hohen Präzisions- und Effizienzanforderungen der modernen Halbleiterfertigung kaum noch erfüllen. Aufgrund seiner einzigartigen Vorteile entwickelt sich das Laserschneiden in diesen Bereichen zunehmend zur bevorzugten Lösung.
Obwohl die Laserschneidtechnologie noch mit Herausforderungen wie hohen Anlagenkosten und Prozesskomplexität konfrontiert ist, machen ihre einzigartigen Vorteile in Bezug auf hohe Präzision und berührungslose Beschädigung sie zu einer wichtigen Entwicklungsrichtung in der Halbleiterfertigung. Mit der Weiterentwicklung der Lasertechnologie und intelligenter Steuerungssysteme dürfte das Laserschneiden die Effizienz und Qualität des Waferschneidens weiter verbessern und so die kontinuierliche Weiterentwicklung der Halbleiterindustrie vorantreiben.
2.3 Plasmaschneidtechnik
Die Plasmaschneidtechnologie hat als neuartiges Verfahren zum Zerteilen von Wafern in den letzten Jahren stark an Bedeutung gewonnen. Diese Technologie nutzt hochenergetische Plasmastrahlen, um Wafer präzise zu schneiden. Durch die Steuerung von Energie, Geschwindigkeit und Schnittweg des Plasmastrahls werden optimale Schneidergebnisse erzielt.
Funktionsprinzip und Vorteile
Beim Plasmaschneiden wird ein energiereicher, heißer Plasmastrahl erzeugt. Dieser erhitzt das Wafermaterial in kürzester Zeit bis zum Schmelz- oder Verdampfungspunkt und ermöglicht so schnelles Schneiden. Im Vergleich zum herkömmlichen mechanischen Schneiden oder Laserschneiden ist Plasmaschneiden schneller und erzeugt eine kleinere Wärmeeinflusszone. Dadurch werden Risse und Beschädigungen beim Schneiden effektiv reduziert.
In der Praxis eignet sich die Plasmaschneidtechnologie besonders gut für die Bearbeitung komplex geformter Wafer. Ihr hochenergetischer, einstellbarer Plasmastrahl schneidet unregelmäßig geformte Wafer problemlos und mit hoher Präzision. Daher ist diese Technologie in der Mikroelektronikfertigung, insbesondere in der kundenspezifischen Kleinserienproduktion hochwertiger Chips, vielversprechend für einen breiten Einsatz.
Herausforderungen und Einschränkungen
Trotz der vielen Vorteile der Plasmaschneidtechnologie gibt es auch einige Herausforderungen.
• Komplexer Prozess: Der Plasmaschneidprozess ist komplex und erfordert hochpräzise Geräte und erfahrene Bediener, um sicherzustellenGenauigkeit und Stabilität beim Schneiden.
• Umweltkontrolle und Sicherheit: Die hohe Temperatur und Energie des Plasmastrahls erfordern strenge Umweltkontroll- und Sicherheitsmaßnahmen, was die Komplexität und die Kosten der Implementierung erhöht.
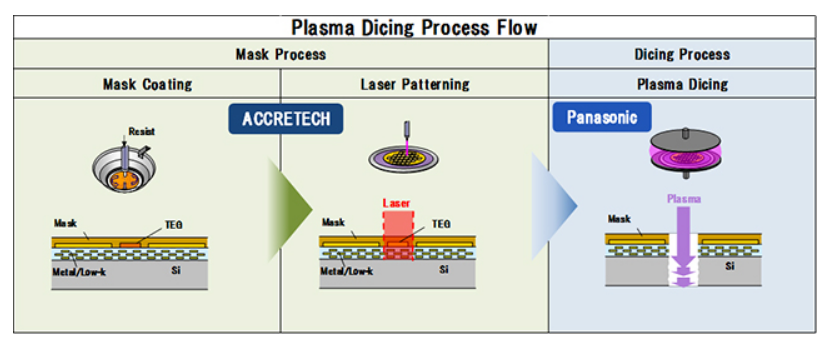
Zukünftige Entwicklungsrichtungen
Mit dem technologischen Fortschritt dürften die Herausforderungen des Plasmaschneidens allmählich überwunden werden. Durch die Entwicklung intelligenterer und stabilerer Schneidanlagen kann die Abhängigkeit von manuellen Arbeitsschritten reduziert und so die Produktionseffizienz gesteigert werden. Gleichzeitig trägt die Optimierung der Prozessparameter und der Schneidumgebung dazu bei, Sicherheitsrisiken und Betriebskosten zu senken.
In der Halbleiterindustrie sind Innovationen in der Waferschneide- und Dicing-Technologie entscheidend für die Entwicklung der Branche. Die Plasmaschneidtechnologie mit ihrer hohen Präzision, Effizienz und der Fähigkeit, komplexe Waferformen zu verarbeiten, hat sich als bedeutender neuer Akteur in diesem Bereich etabliert. Zwar bleiben noch einige Herausforderungen bestehen, doch werden diese durch kontinuierliche technologische Innovationen schrittweise angegangen, was der Halbleiterfertigung neue Möglichkeiten und Chancen eröffnet.
Die Anwendungsmöglichkeiten der Plasmaschneidtechnologie sind vielfältig und es wird erwartet, dass sie in Zukunft eine wichtigere Rolle in der Halbleiterfertigung spielen wird. Durch kontinuierliche technologische Innovation und Optimierung wird das Plasmaschneiden nicht nur bestehende Herausforderungen bewältigen, sondern auch zu einem starken Wachstumsmotor der Halbleiterindustrie werden.
2.4 Schnittqualität und Einflussfaktoren
Die Qualität des Waferschnitts ist entscheidend für die anschließende Chip-Verpackung, die Tests sowie die Gesamtleistung und Zuverlässigkeit des Endprodukts. Häufige Probleme beim Schneiden sind Risse, Absplitterungen und Schnittabweichungen. Diese Probleme werden durch das Zusammenspiel mehrerer Faktoren beeinflusst.
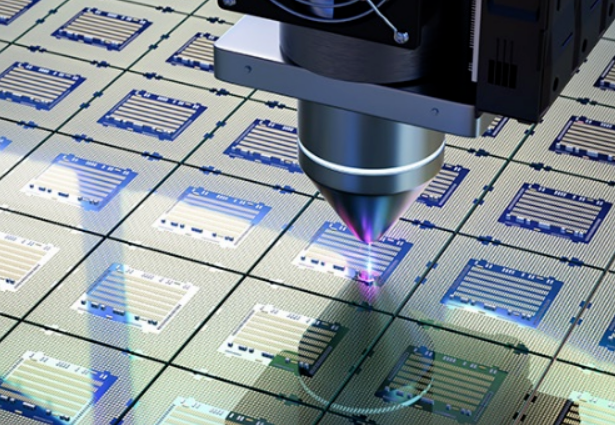
Kategorie | Inhalt | Auswirkungen |
Prozessparameter | Schnittgeschwindigkeit, Vorschub und Schnitttiefe wirken sich direkt auf die Stabilität und Präzision des Schneidprozesses aus. Falsche Einstellungen können zu Spannungskonzentrationen und übermäßiger Wärmeeinflusszone führen, was zu Rissen und Absplitterungen führen kann. Die richtige Anpassung der Parameter an Wafermaterial, -dicke und Schneidanforderungen ist entscheidend für das gewünschte Schneidergebnis. | Die richtigen Prozessparameter gewährleisten einen präzisen Schnitt und verringern das Risiko von Defekten wie Rissen und Absplitterungen. |
Ausstattung und Materialfaktoren | -KlingenqualitätMaterial, Härte und Verschleißfestigkeit der Klinge beeinflussen die Laufruhe des Schneidvorgangs und die Ebenheit der Schnittfläche. Klingen minderer Qualität erhöhen Reibung und thermische Belastung, was zu Rissen oder Absplitterungen führen kann. Die Wahl des richtigen Klingenmaterials ist entscheidend. -KühlmittelleistungKühlmittel senken die Schnitttemperatur, minimieren die Reibung und entfernen Späne. Unwirksames Kühlmittel kann zu hohen Temperaturen und Späneablagerungen führen und so die Schnittqualität und -effizienz beeinträchtigen. Die Auswahl effizienter und umweltfreundlicher Kühlmittel ist entscheidend. | Die Qualität der Klinge beeinflusst die Präzision und Laufruhe des Schnitts. Unwirksames Kühlmittel kann zu schlechter Schnittqualität und -effizienz führen, was die Notwendigkeit einer optimalen Kühlmittelnutzung unterstreicht. |
Prozesskontrolle und Qualitätskontrolle | -Prozesskontrolle: Echtzeitüberwachung und Anpassung wichtiger Schneidparameter, um Stabilität und Konsistenz im Schneidprozess zu gewährleisten. -Qualitätsprüfung: Nach dem Schneiden durchgeführte Sichtprüfungen, Maßmessungen und Tests der elektrischen Leistung helfen dabei, Qualitätsprobleme umgehend zu erkennen und zu beheben und so die Schnittgenauigkeit und -konsistenz zu verbessern. | Eine ordnungsgemäße Prozesskontrolle und Qualitätsprüfung tragen dazu bei, gleichbleibend hochwertige Schneidergebnisse sicherzustellen und potenzielle Probleme frühzeitig zu erkennen. |

Verbesserung der Schnittqualität
Die Verbesserung der Schnittqualität erfordert einen umfassenden Ansatz, der Prozessparameter, Geräte- und Materialauswahl, Prozesskontrolle und Inspektion berücksichtigt. Durch die kontinuierliche Weiterentwicklung von Schneidtechnologien und die Optimierung von Prozessmethoden können Präzision und Stabilität des Waferschneidens weiter verbessert und so die Halbleiterfertigungsindustrie zuverlässiger technisch unterstützt werden.
#03 Handhabung und Prüfung nach dem Schneiden
3.1 Reinigung und Trocknung
Die Reinigungs- und Trocknungsschritte nach dem Waferschneiden sind entscheidend für die Chipqualität und den reibungslosen Ablauf nachfolgender Prozesse. In dieser Phase ist es wichtig, Siliziumreste, Kühlmittelrückstände und andere beim Schneiden entstehende Verunreinigungen gründlich zu entfernen. Ebenso wichtig ist es, sicherzustellen, dass die Chips während des Reinigungsvorgangs nicht beschädigt werden. Nach dem Trocknen muss sichergestellt werden, dass keine Feuchtigkeit auf der Chipoberfläche verbleibt, um Probleme wie Korrosion oder elektrostatische Entladung zu vermeiden.
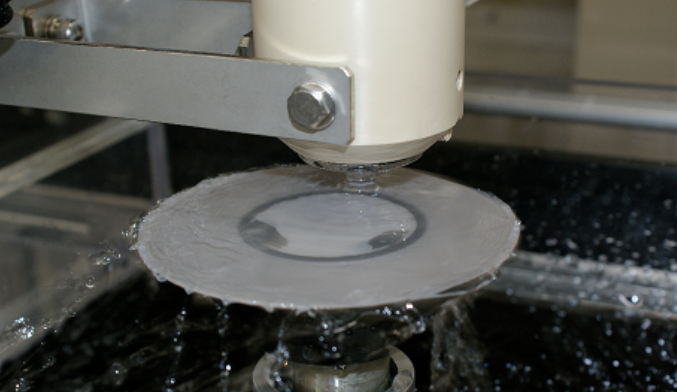
Handhabung nach dem Schneiden: Reinigungs- und Trocknungsprozess
Prozessschritt | Inhalt | Auswirkungen |
Reinigungsprozess | -Verfahren: Verwenden Sie zur Reinigung spezielle Reinigungsmittel und reines Wasser, kombiniert mit Ultraschall- oder mechanischen Bürstentechniken. | Sorgt für eine gründliche Entfernung von Verunreinigungen und verhindert eine Beschädigung der Chips während der Reinigung. |
-Auswahl des Reinigungsmittels: Wählen Sie auf der Grundlage des Wafermaterials und der Art der Verunreinigung, um eine wirksame Reinigung ohne Beschädigung des Chips sicherzustellen. | Die richtige Auswahl des Mittels ist der Schlüssel zu einer effektiven Reinigung und zum Schutz vor Splittern. | |
-Parametersteuerung: Kontrollieren Sie Reinigungstemperatur, -zeit und -konzentration der Reinigungslösung streng, um Qualitätsprobleme durch unsachgemäße Reinigung zu vermeiden. | Kontrollen helfen dabei, eine Beschädigung des Wafers oder das Zurücklassen von Verunreinigungen zu vermeiden und so eine gleichbleibende Qualität sicherzustellen. | |
Trocknungsprozess | -Traditionelle Methoden: Natürliche Lufttrocknung und Heißlufttrocknung, die wenig effizient sind und zur Bildung statischer Elektrizität führen können. | Kann zu längeren Trocknungszeiten und möglichen statischen Problemen führen. |
-Moderne Technologien: Verwenden Sie fortschrittliche Technologien wie Vakuumtrocknung und Infrarottrocknung, um sicherzustellen, dass die Chips schnell trocknen und schädliche Auswirkungen vermieden werden. | Schnellerer und effizienterer Trocknungsprozess, der das Risiko statischer Entladungen oder feuchtigkeitsbedingter Probleme verringert. | |
Auswahl und Wartung der Ausrüstung | -Geräteauswahl: Leistungsstarke Reinigungs- und Trocknungsmaschinen verbessern die Verarbeitungseffizienz und kontrollieren potenzielle Probleme bei der Handhabung präzise. | Hochwertige Maschinen sorgen für eine bessere Verarbeitung und verringern die Fehlerwahrscheinlichkeit beim Reinigen und Trocknen. |
-Gerätewartung: Regelmäßige Inspektionen und Wartungen der Geräte gewährleisten einen optimalen Betriebszustand und garantieren die Chipqualität. | Durch die ordnungsgemäße Wartung werden Geräteausfälle vermieden und eine zuverlässige und qualitativ hochwertige Verarbeitung gewährleistet. |
Reinigung und Trocknung nach dem Schneiden
Die Reinigungs- und Trocknungsschritte nach dem Waferschneiden sind komplexe und heikle Prozesse, die eine sorgfältige Berücksichtigung verschiedener Faktoren erfordern, um das endgültige Verarbeitungsergebnis sicherzustellen. Durch den Einsatz wissenschaftlicher Methoden und strenger Verfahren kann sichergestellt werden, dass jeder Chip die nachfolgenden Verpackungs- und Testphasen in optimalem Zustand erreicht.
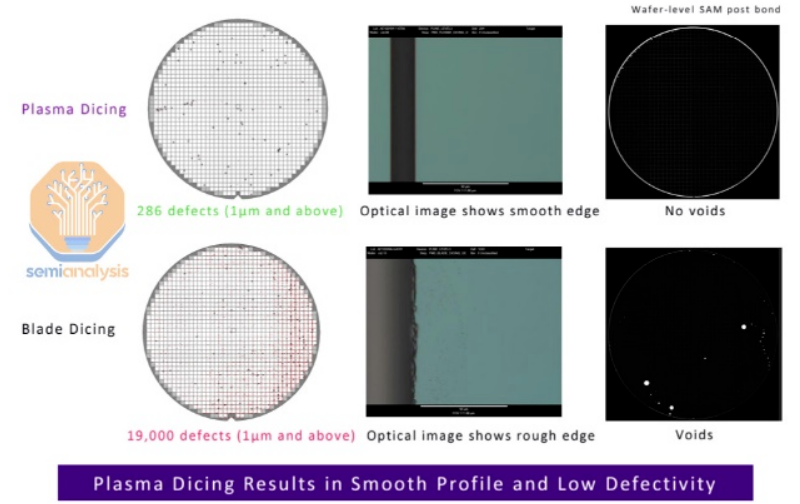
Inspektion und Prüfung nach dem Schneiden
Schritt | Inhalt | Auswirkungen |
Inspektionsschritt | 1.Visuelle Inspektion: Verwenden Sie visuelle oder automatisierte Prüfgeräte, um die Chipoberfläche auf sichtbare Defekte wie Risse, Absplitterungen oder Verunreinigungen zu prüfen. Identifizieren Sie physisch beschädigte Chips schnell, um Ausschuss zu vermeiden. | Hilft, defekte Chips frühzeitig im Prozess zu identifizieren und zu eliminieren und so den Materialverlust zu reduzieren. |
2.Größenmessung: Verwenden Sie Präzisionsmessgeräte, um die Chipabmessungen genau zu messen und sicherzustellen, dass die Schnittgröße den Designspezifikationen entspricht und Leistungsprobleme oder Verpackungsschwierigkeiten vermieden werden. | Stellt sicher, dass die Chips die erforderlichen Größengrenzen einhalten, und verhindert so Leistungseinbußen oder Montageprobleme. | |
3.Elektrische Leistungsprüfung: Bewerten Sie wichtige elektrische Parameter wie Widerstand, Kapazität und Induktivität, um nicht konforme Chips zu identifizieren und sicherzustellen, dass nur leistungsqualifizierte Chips in die nächste Phase gelangen. | Stellt sicher, dass nur funktionsfähige und leistungsgeprüfte Chips im Prozess weiterkommen, wodurch das Risiko von Fehlern in späteren Phasen verringert wird. | |
Testschritt | 1.Funktionstests: Überprüfen Sie, ob die Grundfunktionalität des Chips wie vorgesehen funktioniert, und identifizieren und eliminieren Sie Chips mit Funktionsstörungen. | Stellt sicher, dass die Chips die grundlegenden Betriebsanforderungen erfüllen, bevor mit den späteren Phasen fortgefahren wird. |
2.Zuverlässigkeitstests: Bewerten Sie die Stabilität der Chipleistung bei längerem Gebrauch oder in rauen Umgebungen. Dazu gehören normalerweise Alterung bei hohen Temperaturen, Tests bei niedrigen Temperaturen und Feuchtigkeitstests, um extreme Bedingungen in der realen Welt zu simulieren. | Stellt sicher, dass Chips unter verschiedenen Umgebungsbedingungen zuverlässig funktionieren, und verbessert so die Langlebigkeit und Stabilität des Produkts. | |
3.Kompatibilitätstests: Überprüfen Sie, ob der Chip ordnungsgemäß mit anderen Komponenten oder Systemen funktioniert, und stellen Sie sicher, dass keine Fehler oder Leistungseinbußen aufgrund von Inkompatibilität auftreten. | Gewährleistet einen reibungslosen Betrieb in realen Anwendungen, indem Kompatibilitätsprobleme vermieden werden. |
3.3 Verpackung und Lagerung
Nach dem Waferschneiden sind die Chips ein entscheidendes Ergebnis des Halbleiterherstellungsprozesses. Ihre Verpackungs- und Lagerungsphasen sind daher ebenso wichtig. Sachgemäße Verpackungs- und Lagerungsmaßnahmen sind nicht nur für die Sicherheit und Stabilität der Chips während Transport und Lagerung unerlässlich, sondern auch für eine optimale Unterstützung der nachfolgenden Produktions-, Test- und Verpackungsphasen.
Zusammenfassung der Inspektions- und Testphasen:
Die Inspektions- und Testschritte für Chips nach dem Waferschneiden umfassen verschiedene Aspekte, darunter Sichtprüfung, Größenmessung, elektrische Leistungsprüfung, Funktionsprüfung, Zuverlässigkeitsprüfung und Kompatibilitätsprüfung. Diese Schritte sind miteinander verbunden und ergänzen sich gegenseitig und bilden eine solide Grundlage für Produktqualität und -zuverlässigkeit. Durch strenge Inspektions- und Testverfahren können potenzielle Probleme umgehend erkannt und behoben werden, sodass sichergestellt wird, dass das Endprodukt die Anforderungen und Erwartungen der Kunden erfüllt.
Aspekt | Inhalt |
Verpackungsmaße | 1.Antistatisch: Verpackungsmaterialien sollten über hervorragende antistatische Eigenschaften verfügen, um zu verhindern, dass statische Elektrizität die Geräte beschädigt oder ihre Leistung beeinträchtigt. |
2.Feuchtigkeitsbeständig: Verpackungsmaterialien sollten eine gute Feuchtigkeitsbeständigkeit aufweisen, um Korrosion und eine Verschlechterung der elektrischen Leistung durch Feuchtigkeit zu verhindern. | |
3.Stoßfest: Verpackungsmaterialien sollten eine wirksame Stoßdämpfung bieten, um die Chips während des Transports vor Vibrationen und Stößen zu schützen. | |
Speicherumgebung | 1.Feuchtigkeitskontrolle: Kontrollieren Sie die Luftfeuchtigkeit streng innerhalb eines angemessenen Bereichs, um Feuchtigkeitsaufnahme und Korrosion durch übermäßige Luftfeuchtigkeit oder statische Aufladung durch niedrige Luftfeuchtigkeit zu verhindern. |
2.Sauberkeit: Sorgen Sie für eine saubere Lagerumgebung, um eine Verunreinigung der Chips durch Staub und Verunreinigungen zu vermeiden. | |
3.Temperaturregelung: Legen Sie einen angemessenen Temperaturbereich fest und halten Sie die Temperaturstabilität aufrecht, um eine beschleunigte Alterung durch übermäßige Hitze oder Kondensationsprobleme aufgrund niedriger Temperaturen zu verhindern. | |
Regelmäßige Inspektion | Überprüfen und bewerten Sie gelagerte Chips regelmäßig mithilfe von Sichtprüfungen, Größenmessungen und elektrischen Leistungstests, um potenzielle Probleme rechtzeitig zu erkennen und zu beheben. Planen Sie die Verwendung der Chips basierend auf Lagerdauer und -bedingungen, um sicherzustellen, dass sie in optimalem Zustand eingesetzt werden. |
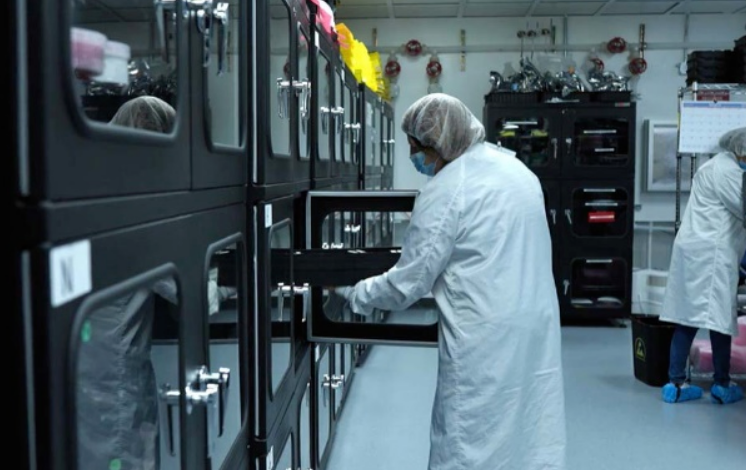
Mikrorisse und Schäden beim Wafer-Dicing stellen eine große Herausforderung in der Halbleiterfertigung dar. Die Schneidspannung ist die Hauptursache für dieses Phänomen, da sie winzige Risse und Schäden auf der Waferoberfläche verursacht, was zu höheren Herstellungskosten und einer verminderten Produktqualität führt.
Um diese Herausforderung zu meistern, ist es entscheidend, die Schnittbelastung zu minimieren und optimierte Schneidtechniken, Werkzeuge und Bedingungen einzusetzen. Die sorgfältige Beachtung von Faktoren wie Klingenmaterial, Schnittgeschwindigkeit, Druck und Kühlmethoden kann dazu beitragen, die Bildung von Mikrorissen zu reduzieren und die Gesamtausbeute des Prozesses zu verbessern. Darüber hinaus werden durch die laufende Forschung an fortschrittlicheren Schneidtechnologien wie dem Laser-Dicing Möglichkeiten zur weiteren Reduzierung dieser Probleme erkundet.
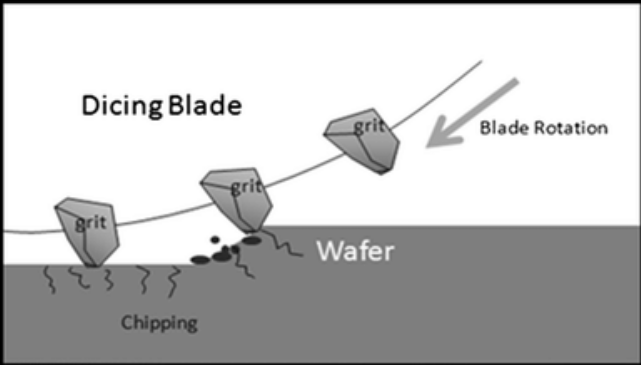
Wafer sind ein fragiles Material und neigen bei mechanischer, thermischer oder chemischer Belastung zu inneren Strukturveränderungen, die zur Bildung von Mikrorissen führen. Diese Risse sind zwar nicht sofort erkennbar, können sich aber im Laufe des Herstellungsprozesses ausweiten und schwerwiegendere Schäden verursachen. Besonders problematisch wird dieses Problem in den nachfolgenden Verpackungs- und Testphasen, wo Temperaturschwankungen und zusätzliche mechanische Belastungen dazu führen können, dass sich diese Mikrorisse zu sichtbaren Brüchen entwickeln und so zum Chipversagen führen können.
Um dieses Risiko zu minimieren, ist es wichtig, den Schneidprozess sorgfältig zu steuern und Parameter wie Schneidgeschwindigkeit, Druck und Temperatur zu optimieren. Der Einsatz weniger aggressiver Schneidverfahren wie Laserschneiden kann die mechanische Belastung des Wafers reduzieren und die Bildung von Mikrorissen minimieren. Zusätzlich können fortschrittliche Inspektionsmethoden wie Infrarot-Scanning oder Röntgenbildgebung während des Waferschneidens helfen, diese Risse im Frühstadium zu erkennen, bevor sie weiteren Schaden anrichten.
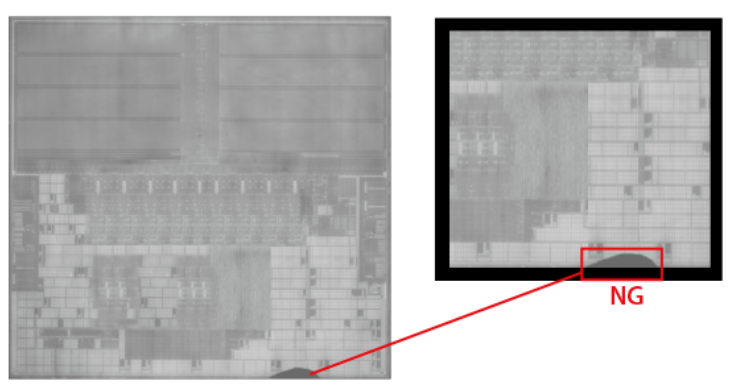
Schäden an der Waferoberfläche stellen beim Dicing-Prozess ein erhebliches Problem dar, da sie die Leistung und Zuverlässigkeit des Chips direkt beeinträchtigen können. Solche Schäden können durch unsachgemäßen Einsatz von Schneidwerkzeugen, falsche Schneidparameter oder Materialfehler im Wafer selbst verursacht werden. Unabhängig von der Ursache können diese Schäden zu Veränderungen des elektrischen Widerstands oder der Kapazität der Schaltung führen und so die Gesamtleistung beeinträchtigen.
Zur Lösung dieser Probleme werden zwei Schlüsselstrategien untersucht:
1.Optimierung von Schneidwerkzeugen und Parametern: Durch die Verwendung schärferer Klingen, die Anpassung der Schnittgeschwindigkeit und die Veränderung der Schnitttiefe kann die Spannungskonzentration während des Schneidvorgangs minimiert und somit das Schadenspotenzial verringert werden.
2.Erforschung neuer Schneidtechnologien: Fortschrittliche Techniken wie Laserschneiden und Plasmaschneiden bieten höhere Präzision und reduzieren potenziell die Beschädigung des Wafers. Diese Technologien werden untersucht, um eine hohe Schnittgenauigkeit bei gleichzeitiger Minimierung der thermischen und mechanischen Belastung des Wafers zu erreichen.
Thermischer Einflussbereich und seine Auswirkungen auf die Leistung
Bei thermischen Schneidverfahren wie Laser- und Plasmaschneiden entsteht durch hohe Temperaturen zwangsläufig eine thermische Einflusszone auf der Waferoberfläche. Dieser Bereich mit seinem signifikanten Temperaturgradienten kann die Materialeigenschaften verändern und so die endgültige Leistung des Chips beeinträchtigen.
Auswirkungen der thermisch beeinflussten Zone (TAZ):
Veränderungen der Kristallstruktur: Bei hohen Temperaturen können sich Atome im Wafermaterial neu anordnen und die Kristallstruktur verzerren. Diese Verzerrung schwächt das Material und verringert seine mechanische Festigkeit und Stabilität. Dies erhöht das Risiko eines Chipausfalls während des Betriebs.
Änderungen der elektrischen Eigenschaften: Hohe Temperaturen können die Ladungsträgerkonzentration und -beweglichkeit in Halbleitermaterialien verändern und so die elektrische Leitfähigkeit und die Stromübertragungseffizienz des Chips beeinträchtigen. Diese Veränderungen können zu einer Verschlechterung der Chipleistung führen und ihn möglicherweise für seinen vorgesehenen Zweck ungeeignet machen.
Um diese Effekte zu mildern, sind die Kontrolle der Temperatur während des Schneidens, die Optimierung der Schneidparameter und die Erforschung von Methoden wie Kühlstrahlen oder Nachbearbeitungsbehandlungen wichtige Strategien, um das Ausmaß der thermischen Auswirkungen zu verringern und die Materialintegrität zu erhalten.
Insgesamt stellen sowohl Mikrorisse als auch thermische Einflusszonen entscheidende Herausforderungen in der Wafer-Dicing-Technologie dar. Um die Qualität von Halbleiterprodukten zu verbessern und ihre Wettbewerbsfähigkeit auf dem Markt zu steigern, sind kontinuierliche Forschung sowie technologische Fortschritte und Qualitätskontrollmaßnahmen erforderlich.
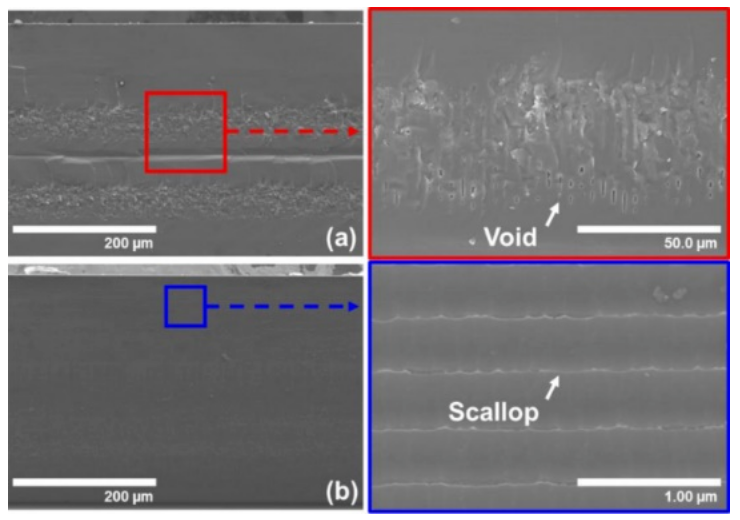
Maßnahmen zur Kontrolle der thermischen Einflusszone:
Optimierung der Schneidprozessparameter: Durch Reduzierung der Schneidgeschwindigkeit und -leistung kann die Größe der Wärmeeinflusszone (TAZ) effektiv minimiert werden. Dies trägt dazu bei, die während des Schneidvorgangs erzeugte Wärmemenge zu kontrollieren, die sich direkt auf die Materialeigenschaften des Wafers auswirkt.
Fortschrittliche Kühltechnologien: Der Einsatz von Technologien wie Flüssigstickstoffkühlung und Mikrofluidikkühlung kann den thermischen Einflussbereich deutlich einschränken. Diese Kühlmethoden tragen zu einer effizienteren Wärmeableitung bei, wodurch die Materialeigenschaften des Wafers erhalten bleiben und thermische Schäden minimiert werden.
Materialauswahl: Forscher erforschen neue Materialien wie Kohlenstoffnanoröhren und Graphen, die über eine hervorragende Wärmeleitfähigkeit und mechanische Festigkeit verfügen. Diese Materialien können die thermische Aufprallzone reduzieren und gleichzeitig die Gesamtleistung der Chips verbessern.
Zusammenfassend lässt sich sagen, dass die thermische Einflusszone zwar eine unvermeidliche Folge thermischer Schneidtechnologien ist, sich aber durch optimierte Verarbeitungstechniken und Materialauswahl effektiv kontrollieren lässt. Zukünftige Forschung wird sich voraussichtlich auf die Feinabstimmung und Automatisierung thermischer Schneidprozesse konzentrieren, um ein effizienteres und präziseres Wafer-Dicing zu erreichen.

Balance-Strategie:
Das optimale Gleichgewicht zwischen Waferausbeute und Produktionseffizienz ist in der Wafer-Dicing-Technologie eine ständige Herausforderung. Hersteller müssen verschiedene Faktoren wie Marktnachfrage, Produktionskosten und Produktqualität berücksichtigen, um eine rationale Produktionsstrategie und Prozessparameter zu entwickeln. Gleichzeitig sind die Einführung moderner Schneidegeräte, die Verbesserung der Bedienerkompetenz und eine verbesserte Qualitätskontrolle der Rohstoffe unerlässlich, um die Ausbeute bei gleichzeitiger Steigerung der Produktionseffizienz zu halten oder sogar zu verbessern.
Zukünftige Herausforderungen und Chancen:
Mit dem Fortschritt der Halbleitertechnologie stehen dem Waferschneiden neue Herausforderungen und Chancen gegenüber. Mit sinkenden Chipgrößen und zunehmender Integration steigen die Anforderungen an Schneidpräzision und -qualität deutlich. Gleichzeitig liefern neue Technologien neue Ideen für die Entwicklung von Waferschneidetechniken. Hersteller müssen die Marktdynamik und technologischen Trends im Auge behalten und Produktionsstrategien und Prozessparameter kontinuierlich anpassen und optimieren, um Marktveränderungen und technologischen Anforderungen gerecht zu werden.
Zusammenfassend lässt sich sagen, dass Hersteller durch die Integration von Überlegungen zur Marktnachfrage, zu Produktionskosten und Produktqualität sowie durch die Einführung moderner Geräte und Technologien, die Verbesserung der Fähigkeiten der Bediener und eine verstärkte Rohstoffkontrolle das beste Gleichgewicht zwischen Waferausbeute und Produktionseffizienz beim Wafer-Dicing erreichen können, was zu einer effizienten und qualitativ hochwertigen Herstellung von Halbleiterprodukten führt.
Zukunftsaussichten:
Dank des rasanten technologischen Fortschritts entwickelt sich die Halbleitertechnologie in beispiellosem Tempo weiter. Als entscheidender Schritt in der Halbleiterfertigung steht die Waferschneidetechnologie vor spannenden neuen Entwicklungen. Zukünftig wird erwartet, dass die Waferschneidetechnologie deutliche Verbesserungen bei Präzision, Effizienz und Kosten erzielt und so dem weiteren Wachstum der Halbleiterindustrie neuen Schwung verleiht.
Steigerung der Präzision:
Im Streben nach höherer Präzision wird die Waferschneidetechnologie die Grenzen bestehender Verfahren kontinuierlich erweitern. Durch die eingehende Untersuchung der physikalischen und chemischen Mechanismen des Schneidprozesses und die präzise Steuerung der Schneidparameter werden feinere Schneidergebnisse erzielt, um den zunehmend komplexeren Anforderungen des Schaltungsdesigns gerecht zu werden. Darüber hinaus wird die Erforschung neuer Materialien und Schneidverfahren Ausbeute und Qualität deutlich verbessern.
Effizienzsteigerung:
Neue Wafer-Schneidanlagen setzen auf intelligentes und automatisiertes Design. Durch die Einführung fortschrittlicher Steuerungssysteme und Algorithmen können die Anlagen die Schneidparameter automatisch an unterschiedliche Materialien und Designanforderungen anpassen und so die Produktionseffizienz deutlich steigern. Innovationen wie die Mehrwafer-Schneidtechnologie und Systeme zum schnellen Klingenwechsel werden einen entscheidenden Beitrag zur Effizienzsteigerung leisten.
Kosten senken:
Kostensenkung ist ein zentraler Aspekt der Entwicklung der Waferschneidtechnologie. Mit der Entwicklung neuer Materialien und Schneideverfahren lassen sich die Geräte- und Wartungskosten effektiv kontrollieren. Optimierte Produktionsprozesse und reduzierte Ausschussraten tragen zusätzlich zur Abfallreduzierung bei und führen so zu niedrigeren Gesamtproduktionskosten.
Intelligente Fertigung und IoT:
Die Integration von Smart Manufacturing und dem Internet der Dinge (IoT) wird die Waferschneidetechnologie grundlegend verändern. Durch die Vernetzung und den Datenaustausch zwischen Geräten kann jeder Schritt des Produktionsprozesses in Echtzeit überwacht und optimiert werden. Dies verbessert nicht nur die Produktionseffizienz und Produktqualität, sondern bietet Unternehmen auch präzisere Marktprognosen und Entscheidungshilfen.
Die Waferschneidetechnologie wird in Zukunft deutliche Fortschritte in puncto Präzision, Effizienz und Kosten erzielen. Diese Fortschritte werden die weitere Entwicklung der Halbleiterindustrie vorantreiben und der Gesellschaft weitere technologische Innovationen und Annehmlichkeiten bringen.
Veröffentlichungszeit: 19. November 2024