Im boomenden Entwicklungsprozess der Halbleiterindustrie werden polierte EinkristalleSiliziumwaferspielen eine entscheidende Rolle. Sie dienen als Grundmaterial für die Herstellung verschiedener mikroelektronischer Geräte. Von komplexen und präzisen integrierten Schaltkreisen bis hin zu Hochgeschwindigkeits-Mikroprozessoren und multifunktionalen Sensoren – polierte EinkristalleSiliziumwafersind unerlässlich. Die Unterschiede in Leistung und Spezifikationen wirken sich direkt auf die Qualität und Leistung der Endprodukte aus. Nachfolgend finden Sie die gängigen Spezifikationen und Parameter polierter Einkristall-Siliziumwafer:
Durchmesser: Die Größe von Halbleiter-Einkristall-Siliziumwafern wird anhand ihres Durchmessers gemessen. Sie sind in verschiedenen Spezifikationen erhältlich. Gängige Durchmesser sind 2 Zoll (50,8 mm), 3 Zoll (76,2 mm), 4 Zoll (100 mm), 5 Zoll (125 mm), 6 Zoll (150 mm), 8 Zoll (200 mm), 12 Zoll (300 mm) und 18 Zoll (450 mm). Verschiedene Durchmesser eignen sich für verschiedene Produktionsbedürfnisse und Prozessanforderungen. Beispielsweise werden Wafer mit kleinerem Durchmesser häufig für spezielle mikroelektronische Geräte in kleiner Stückzahl verwendet, während Wafer mit größerem Durchmesser eine höhere Produktionseffizienz und Kostenvorteile bei der Herstellung integrierter Schaltkreise im großen Maßstab aufweisen. Die Oberflächenanforderungen werden in einseitig poliert (SSP) und doppelseitig poliert (DSP) unterteilt. Einseitig polierte Wafer werden für Geräte verwendet, die eine hohe Ebenheit auf einer Seite erfordern, wie z. B. bestimmte Sensoren. Doppelseitig polierte Wafer werden häufig für integrierte Schaltkreise und andere Produkte verwendet, die eine hohe Präzision auf beiden Oberflächen erfordern. Oberflächenanforderung (Finish): Einseitig poliertes SSP / Doppelseitig poliertes DSP.
Typ/Dotierstoff: (1) N-Typ-Halbleiter: Werden Fremdatome in den intrinsischen Halbleiter eingebracht, verändern diese dessen Leitfähigkeit. Werden beispielsweise fünfwertige Elemente wie Stickstoff (N), Phosphor (P), Arsen (As) oder Antimon (Sb) hinzugefügt, bilden deren Valenzelektronen kovalente Bindungen mit den Valenzelektronen der umgebenden Siliziumatome, wodurch ein zusätzliches Elektron entsteht, das nicht durch eine kovalente Bindung gebunden ist. Dadurch ist die Elektronenkonzentration größer als die Lochkonzentration, und es entsteht ein N-Typ-Halbleiter, auch Elektronen-Halbleiter genannt. N-Typ-Halbleiter sind entscheidend für die Herstellung von Geräten, die Elektronen als Hauptladungsträger benötigen, wie beispielsweise bestimmte Leistungsbauelemente. (2) P-Typ-Halbleiter: Werden dreiwertige Fremdelemente wie Bor (B), Gallium (Ga) oder Indium (In) in den Siliziumhalbleiter eingebracht, bilden die Valenzelektronen der Fremdatome kovalente Bindungen mit den umgebenden Siliziumatomen. Ihnen fehlt jedoch mindestens ein Valenzelektron, sodass keine vollständige kovalente Bindung entstehen kann. Dies führt zu einer größeren Lochkonzentration als die Elektronenkonzentration, wodurch ein P-Typ-Halbleiter entsteht, auch Lochtyp-Halbleiter genannt. P-Typ-Halbleiter spielen eine Schlüsselrolle bei der Herstellung von Bauelementen, bei denen Löcher als Hauptladungsträger dienen, wie beispielsweise Dioden und bestimmten Transistoren.
Spezifischer Widerstand: Der spezifische Widerstand ist eine wichtige physikalische Größe, die die elektrische Leitfähigkeit polierter Einkristall-Siliziumwafer misst. Sein Wert spiegelt die Leitfähigkeit des Materials wider. Je niedriger der spezifische Widerstand, desto besser ist die Leitfähigkeit des Siliziumwafers; umgekehrt gilt: Je höher der spezifische Widerstand, desto schlechter die Leitfähigkeit. Der spezifische Widerstand von Siliziumwafern wird durch ihre inhärenten Materialeigenschaften bestimmt, wobei auch die Temperatur einen erheblichen Einfluss hat. Im Allgemeinen steigt der spezifische Widerstand von Siliziumwafern mit der Temperatur. In der Praxis stellen verschiedene mikroelektronische Geräte unterschiedliche Anforderungen an den spezifischen Widerstand von Siliziumwafern. Beispielsweise erfordern Wafer für die Herstellung integrierter Schaltkreise eine präzise Widerstandskontrolle, um eine stabile und zuverlässige Geräteleistung zu gewährleisten.
Orientierung: Die Kristallorientierung des Wafers stellt die kristallografische Richtung des Siliziumgitters dar, typischerweise angegeben durch Miller-Indizes wie (100), (110), (111) usw. Unterschiedliche Kristallorientierungen haben unterschiedliche physikalische Eigenschaften, wie beispielsweise die Liniendichte, die je nach Orientierung variiert. Dieser Unterschied kann die Leistung des Wafers in nachfolgenden Verarbeitungsschritten und die endgültige Leistung mikroelektronischer Geräte beeinträchtigen. Im Herstellungsprozess kann die Auswahl eines Siliziumwafers mit der passenden Orientierung für unterschiedliche Geräteanforderungen die Geräteleistung optimieren, die Produktionseffizienz verbessern und die Produktqualität steigern.
Flachkante/Kerbe: Die Flachkante (Flat) oder V-Kerbe (Notch) am Rand des Siliziumwafers spielt eine entscheidende Rolle bei der Ausrichtung der Kristallorientierung und ist ein wichtiges Erkennungsmerkmal bei der Herstellung und Verarbeitung des Wafers. Wafer mit unterschiedlichen Durchmessern entsprechen unterschiedlichen Standards für die Länge der Flachkante bzw. Kerbe. Die Ausrichtungskanten werden in primäre und sekundäre Flachkanten unterteilt. Die primäre Flachkante dient hauptsächlich der Bestimmung der grundlegenden Kristallorientierung und der Verarbeitungsreferenz des Wafers, während die sekundäre Flachkante zusätzlich zur präzisen Ausrichtung und Verarbeitung beiträgt und so eine präzise Verarbeitung und Konsistenz des Wafers in der gesamten Produktionslinie gewährleistet.
Dicke: Die Dicke eines Wafers wird üblicherweise in Mikrometern (μm) angegeben, wobei gängige Dickenbereiche zwischen 100 μm und 1000 μm liegen. Wafer unterschiedlicher Dicke eignen sich für verschiedene Arten mikroelektronischer Bauelemente. Dünnere Wafer (z. B. 100 μm – 300 μm) werden häufig für die Chipherstellung verwendet, die eine strenge Dickenkontrolle erfordert, um Größe und Gewicht des Chips zu reduzieren und die Integrationsdichte zu erhöhen. Dickere Wafer (z. B. 500 μm – 1000 μm) werden häufig in Bauelementen eingesetzt, die eine höhere mechanische Festigkeit erfordern, wie z. B. Leistungshalbleiterbauelemente, um die Stabilität im Betrieb zu gewährleisten.
Oberflächenrauheit: Die Oberflächenrauheit ist einer der wichtigsten Parameter zur Bewertung der Waferqualität, da sie die Haftung zwischen dem Wafer und den anschließend aufgebrachten Dünnschichtmaterialien sowie die elektrische Leistung des Geräts direkt beeinflusst. Sie wird üblicherweise als quadratischer Mittelwert der Rauheit (RMS) in nm angegeben. Eine geringere Oberflächenrauheit bedeutet eine glattere Waferoberfläche, was Phänomene wie Elektronenstreuung reduziert und die Leistung und Zuverlässigkeit des Geräts verbessert. In modernen Halbleiterfertigungsprozessen werden die Anforderungen an die Oberflächenrauheit immer strenger, insbesondere bei der Herstellung hochwertiger integrierter Schaltkreise, wo die Oberflächenrauheit auf wenige Nanometer oder sogar weniger begrenzt werden muss.
Gesamtdickenvariation (TTV): Die Gesamtdickenvariation bezeichnet die Differenz zwischen der an mehreren Punkten der Waferoberfläche gemessenen maximalen und minimalen Dicke, typischerweise in μm angegeben. Eine hohe TTV kann zu Abweichungen in Prozessen wie der Fotolithografie und dem Ätzen führen und so die Leistungskonsistenz und Ausbeute des Geräts beeinträchtigen. Daher ist die Kontrolle der TTV während der Waferherstellung ein wichtiger Schritt zur Sicherstellung der Produktqualität. Für die hochpräzise Herstellung mikroelektronischer Geräte muss die TTV typischerweise im Bereich weniger Mikrometer liegen.
Krümmung: Unter Krümmung versteht man die Abweichung zwischen der Waferoberfläche und der idealen ebenen Fläche, typischerweise gemessen in μm. Wafer mit übermäßiger Krümmung können bei der Weiterverarbeitung brechen oder ungleichmäßiger Belastung ausgesetzt sein, was die Produktionseffizienz und Produktqualität beeinträchtigt. Insbesondere bei Prozessen, die eine hohe Ebenheit erfordern, wie z. B. der Fotolithografie, muss die Krümmung innerhalb eines bestimmten Bereichs kontrolliert werden, um die Genauigkeit und Konsistenz des fotolithografischen Musters zu gewährleisten.
Warp: Warp bezeichnet die Abweichung zwischen der Waferoberfläche und der idealen Kugelform, ebenfalls in μm gemessen. Ähnlich wie die Krümmung ist Warp ein wichtiger Indikator für die Waferebenheit. Übermäßiger Warp beeinträchtigt nicht nur die Platzierungsgenauigkeit des Wafers in der Verarbeitungsanlage, sondern kann auch Probleme beim Chip-Verpackungsprozess verursachen, wie z. B. eine schlechte Verbindung zwischen Chip und Verpackungsmaterial, was wiederum die Zuverlässigkeit des Geräts beeinträchtigt. In der High-End-Halbleiterfertigung werden die Warp-Anforderungen immer strenger, um den Anforderungen fortschrittlicher Chip-Fertigungs- und Verpackungsprozesse gerecht zu werden.
Kantenprofil: Das Kantenprofil eines Wafers ist entscheidend für dessen spätere Verarbeitung und Handhabung. Es wird typischerweise durch die Randsperrzone (EEZ) definiert, die den Abstand vom Waferrand definiert, in dem keine Bearbeitung zulässig ist. Ein richtig gestaltetes Kantenprofil und eine präzise EEZ-Kontrolle tragen dazu bei, Kantendefekte, Spannungskonzentrationen und andere Probleme während der Verarbeitung zu vermeiden und so die Gesamtqualität und Ausbeute des Wafers zu verbessern. Bei einigen fortschrittlichen Fertigungsprozessen muss die Kantenprofilpräzision im Submikrometerbereich liegen.
Partikelanzahl: Anzahl und Größenverteilung der Partikel auf der Waferoberfläche beeinflussen die Leistung mikroelektronischer Bauelemente maßgeblich. Zu viele oder zu große Partikel können zu Geräteausfällen wie Kurzschlüssen oder Leckagen führen und so die Produktausbeute reduzieren. Daher wird die Partikelanzahl üblicherweise durch Zählen der Partikel pro Flächeneinheit gemessen, beispielsweise der Anzahl der Partikel größer als 0,3 μm. Eine strenge Kontrolle der Partikelanzahl während der Waferherstellung ist eine wesentliche Maßnahme zur Sicherstellung der Produktqualität. Fortschrittliche Reinigungstechnologien und eine saubere Produktionsumgebung werden eingesetzt, um die Partikelkontamination auf der Waferoberfläche zu minimieren.
Verwandte Produktion
Einkristalliner Siliziumwafer Si-Substrattyp N/P Optionaler Siliziumkarbidwafer
FZ CZ Si-Wafer auf Lager 12-Zoll-Silizium-Wafer Prime oder Test
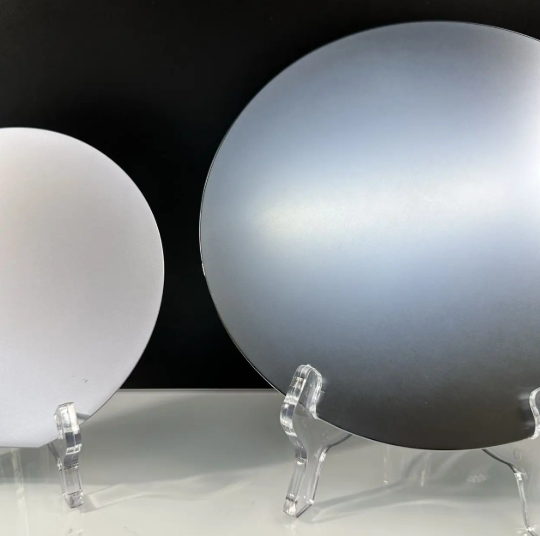
Veröffentlichungszeit: 18. April 2025