Einführung in Siliziumkarbid
Siliziumkarbid (SiC) ist ein Verbindungshalbleitermaterial aus Kohlenstoff und Silizium und eines der idealen Materialien für die Herstellung von Geräten mit hohen Temperaturen, hohen Frequenzen, hoher Leistung und hoher Spannung. Im Vergleich zu herkömmlichem Silizium (Si) ist die Bandlücke von Siliziumkarbid dreimal so groß wie die von Silizium. Die Wärmeleitfähigkeit ist vier- bis fünfmal so hoch wie die von Silizium; die Durchbruchspannung ist acht- bis zehnmal so hoch wie die von Silizium; die elektronische Sättigungsdriftrate ist zwei- bis dreimal so hoch wie die von Silizium, was den Anforderungen der modernen Industrie an hohe Leistung, hohe Spannung und hohe Frequenz gerecht wird. Es wird hauptsächlich zur Herstellung von Hochgeschwindigkeits-, Hochfrequenz-, Hochleistungs- und lichtemittierenden elektronischen Komponenten verwendet. Zu den nachgelagerten Anwendungsfeldern gehören Smart Grid, Fahrzeuge mit alternativer Energie, Photovoltaik-Windkraft, 5G-Kommunikation usw. Siliziumkarbiddioden und MOSFETs werden kommerziell eingesetzt.
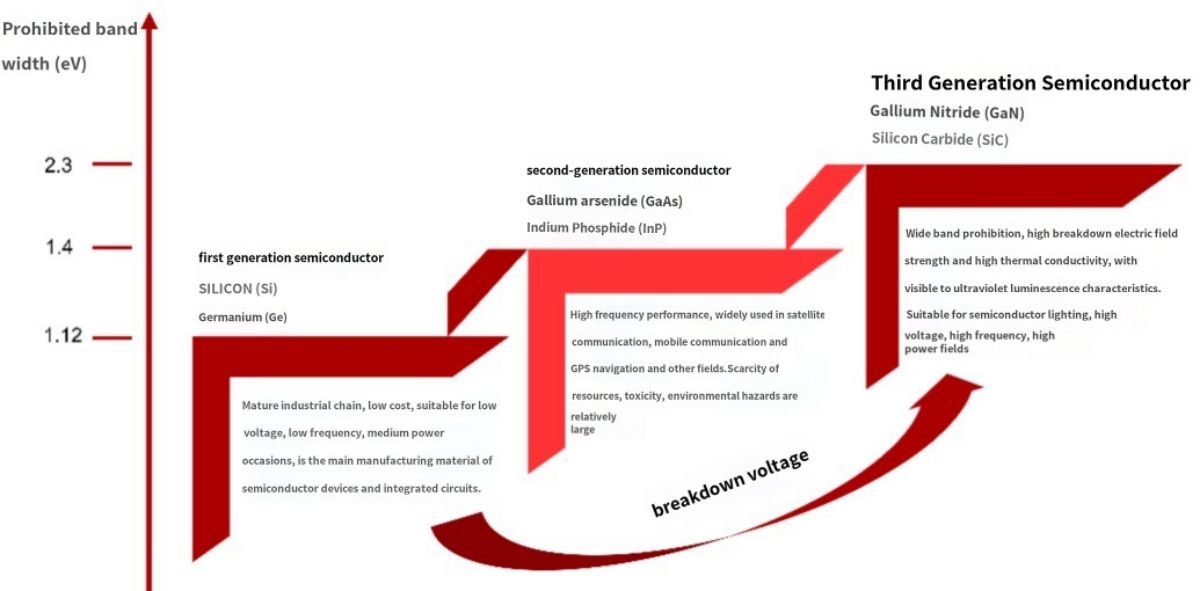
Hohe Temperaturbeständigkeit. Die Bandlücke von Siliziumkarbid ist zwei- bis dreimal so groß wie die von Silizium. Elektronen können bei hohen Temperaturen nur schwer übertragen werden und halten höheren Betriebstemperaturen stand. Die Wärmeleitfähigkeit von Siliziumkarbid ist vier- bis fünfmal so hoch wie die von Silizium. Dadurch wird die Wärmeableitung des Geräts erleichtert und die Betriebstemperaturgrenze erhöht. Die hohe Temperaturbeständigkeit kann die Leistungsdichte deutlich erhöhen und gleichzeitig die Anforderungen an das Kühlsystem reduzieren, wodurch das Terminal leichter und kleiner wird.
Hohem Druck standhalten. Die elektrische Durchbruchfeldstärke von Siliziumkarbid ist zehnmal so hoch wie die von Silizium, sodass es höheren Spannungen standhält und sich besser für Hochspannungsgeräte eignet.
Hochfrequenzbeständigkeit. Siliziumkarbid weist eine gesättigte Elektronendriftrate auf, die doppelt so hoch ist wie die von Silizium, wodurch während des Abschaltvorgangs kein Stromrückfluss auftritt. Dies kann die Schaltfrequenz des Geräts effektiv verbessern und die Miniaturisierung des Geräts ermöglichen.
Geringer Energieverlust. Im Vergleich zu Siliziummaterial weist Siliziumkarbid einen sehr niedrigen Einschaltwiderstand und geringe Einschaltverluste auf. Gleichzeitig reduziert die hohe Bandlückenbreite von Siliziumkarbid den Leckstrom und den Leistungsverlust erheblich. Darüber hinaus tritt beim Abschaltvorgang kein Stromnachlaufphänomen auf, und der Schaltverlust ist gering.
Siliziumkarbid-Industriekette
Es umfasst hauptsächlich Substrat, Epitaxie, Gerätedesign, Herstellung, Versiegelung usw. Vom Material Siliziumkarbid bis zum Halbleiter-Leistungsgerät durchläuft es Prozesse wie Einkristallwachstum, Ingot-Schneiden, epitaktisches Wachstum, Waferdesign, Herstellung, Verpackung und mehr. Nach der Synthese von Siliziumkarbidpulver wird zunächst der Siliziumkarbid-Ingot hergestellt, dann wird durch Schneiden, Schleifen und Polieren das Siliziumkarbid-Substrat gewonnen und durch epitaktisches Wachstum die epitaktische Schicht erhalten. Der epitaktische Wafer wird durch Lithografie, Ätzen, Ionenimplantation, Metallpassivierung und andere Prozesse aus Siliziumkarbid hergestellt, der Wafer wird in Matrizen geschnitten, das Gerät wird verpackt, das Gerät wird in eine spezielle Hülle integriert und zu einem Modul zusammengebaut.
Vorgelagert in der Industriekette 1: Substrat - Kristallwachstum ist das Kernprozessglied
Siliziumkarbidsubstrate machen etwa 47 % der Kosten von Siliziumkarbidgeräten aus, stellen die höchsten technischen Hürden bei der Herstellung dar und sind der größte Wert. Sie sind der Kern der zukünftigen großtechnischen Industrialisierung von SiC.
Aus Sicht der Unterschiede in den elektrochemischen Eigenschaften können Siliziumkarbid-Substrate in leitfähige Substrate (spezifischer Widerstandsbereich 15–30 mΩ·cm) und halbisolierte Substrate (spezifischer Widerstand über 105 Ω·cm) unterteilt werden. Diese beiden Substratarten werden nach epitaktischem Wachstum zur Herstellung diskreter Geräte wie Leistungsbauelementen bzw. Hochfrequenzbauelementen verwendet. Halbisolierte Siliziumkarbid-Substrate werden hauptsächlich zur Herstellung von Galliumnitrid-HF-Geräten, photoelektrischen Geräten usw. verwendet. Durch das Züchten einer Gan-Epitaxieschicht auf einem halbisolierten SIC-Substrat wird die SiC-Epitaxieplatte hergestellt, die weiter zu HEMT-Gan-Isonitrid-HF-Geräten verarbeitet werden kann. Leitfähige Siliziumkarbid-Substrate werden hauptsächlich zur Herstellung von Leistungsbauelementen verwendet. Anders als beim herkömmlichen Herstellungsprozess von Silizium-Leistungsbauelementen kann das Siliziumkarbid-Leistungsbauelement nicht direkt auf dem Siliziumkarbid-Substrat hergestellt werden. Die Siliziumkarbid-Epitaxieschicht muss auf dem leitfähigen Substrat gezüchtet werden, um die Siliziumkarbid-Epitaxieplatte zu erhalten, und die Epitaxieschicht wird auf der Schottky-Diode, dem MOSFET, dem IGBT und anderen Leistungsbauelementen hergestellt.
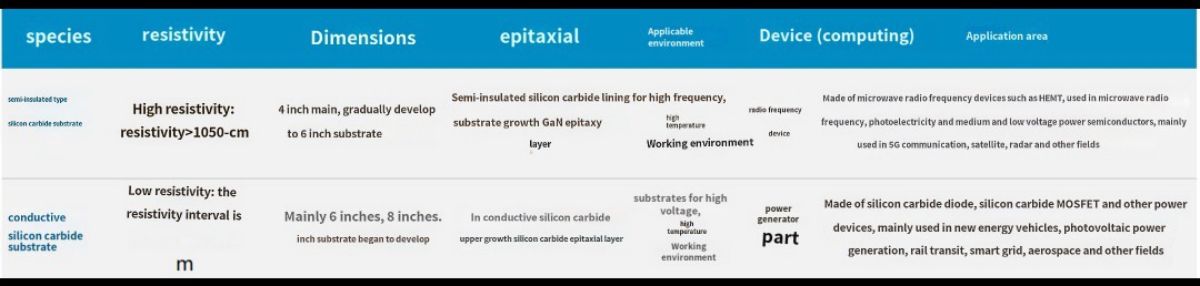
Siliziumkarbidpulver wurde aus hochreinem Kohlenstoffpulver und hochreinem Siliziumpulver synthetisiert. Siliziumkarbidbarren unterschiedlicher Größe wurden unter einem speziellen Temperaturfeld gezüchtet. Anschließend wurde durch mehrere Verarbeitungsprozesse ein Siliziumkarbidsubstrat hergestellt. Der Kernprozess umfasst:
Rohstoffsynthese: Das hochreine Siliziumpulver und der Toner werden gemäß der Formel gemischt. Die Reaktion wird in der Reaktionskammer bei hohen Temperaturen über 2000 °C durchgeführt, um Siliziumkarbidpartikel mit spezifischem Kristalltyp und spezifischer Partikelgröße zu synthetisieren. Anschließend werden durch Zerkleinern, Sieben, Reinigen und andere Prozesse die Anforderungen an hochreine Siliziumkarbidpulver-Rohstoffe erfüllt.
Das Kristallwachstum ist der Kernprozess bei der Herstellung von Siliziumkarbidsubstraten und bestimmt deren elektrische Eigenschaften. Die wichtigsten Methoden für das Kristallwachstum sind derzeit die physikalische Gasphasenabscheidung (PVT), die chemische Gasphasenabscheidung bei hohen Temperaturen (HT-CVD) und die Flüssigphasenepitaxie (LPE). Unter diesen ist die PVT-Methode derzeit die gängigste Methode für das kommerzielle Wachstum von SiC-Substraten. Sie ist technisch am weitesten fortgeschritten und wird in der Technik am häufigsten eingesetzt.
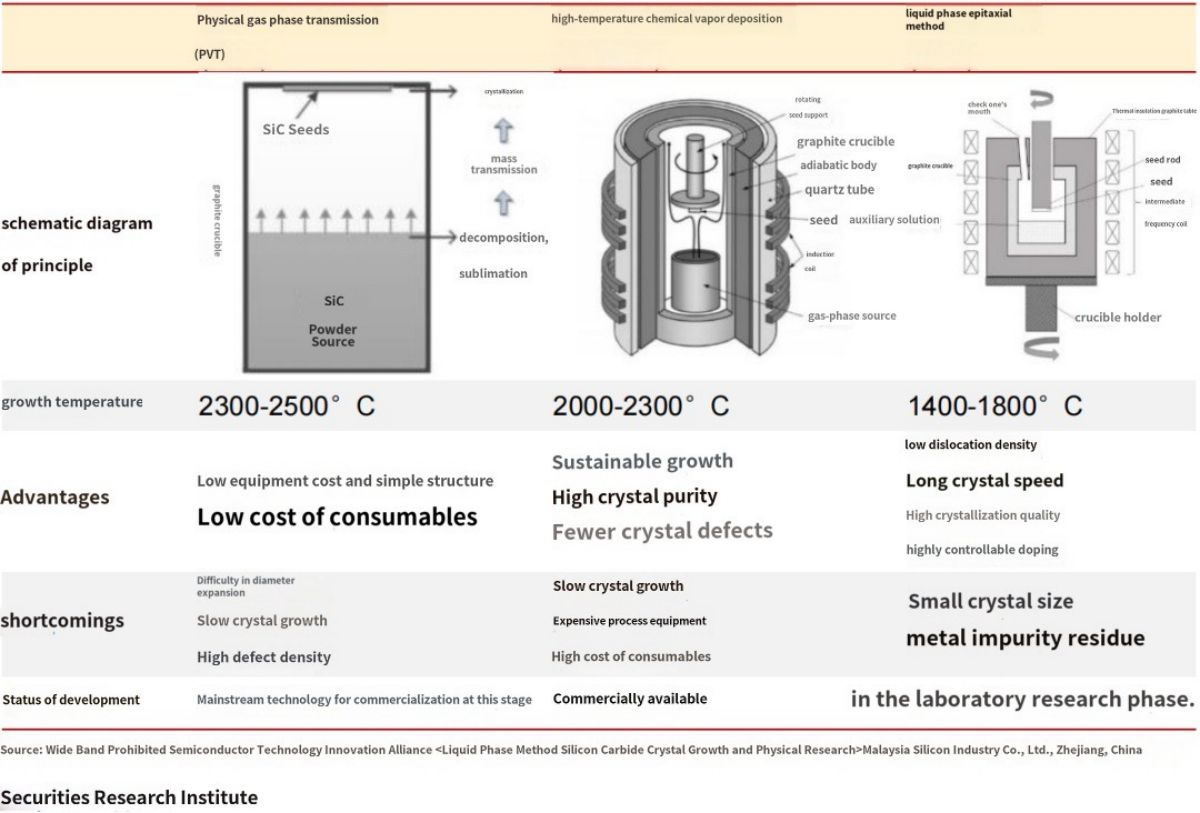
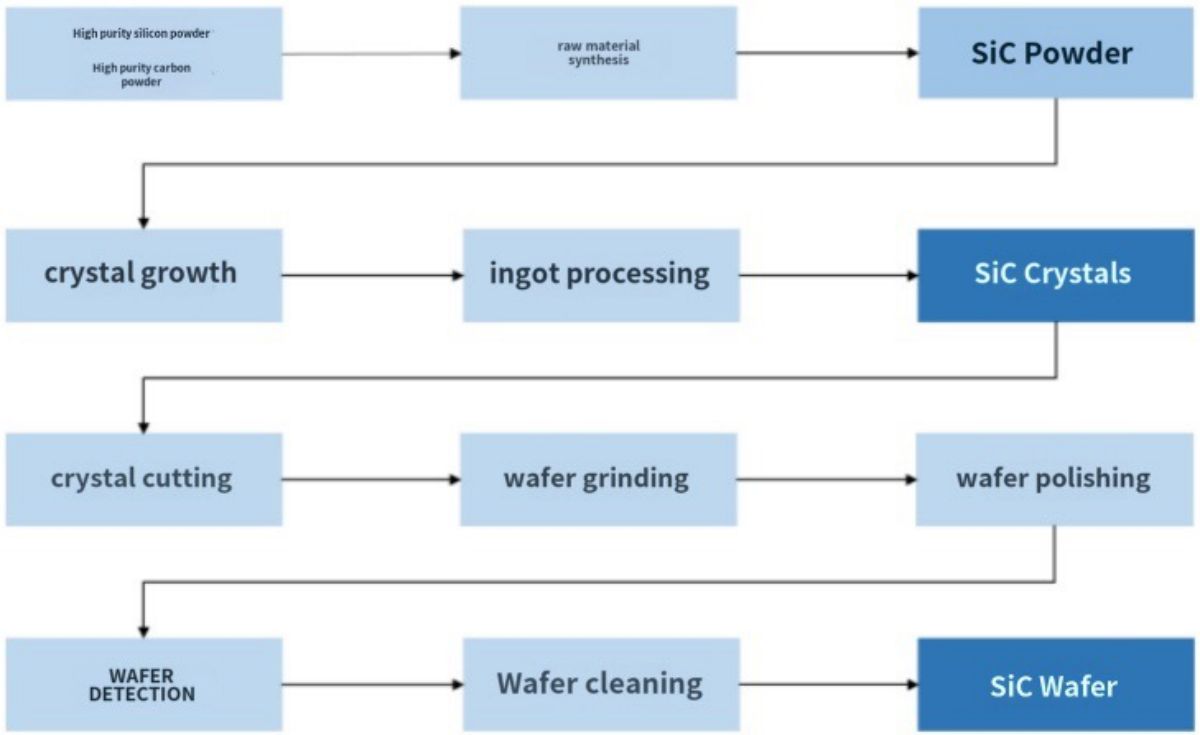
Die Herstellung von SiC-Substraten ist schwierig, was zu ihrem hohen Preis führt
Die Temperaturfeldkontrolle ist schwierig: Für das Wachstum von Si-Kristallstäben sind nur 1500 °C erforderlich, während SiC-Kristallstäbe bei Temperaturen über 2000 °C gezüchtet werden müssen. Es gibt über 250 SiC-Isomere. Die wichtigste 4H-SiC-Einkristallstruktur für die Produktion von Leistungsbauelementen führt jedoch ohne präzise Kontrolle zu anderen Kristallstrukturen. Außerdem bestimmt der Temperaturgradient im Tiegel die Geschwindigkeit des SiC-Sublimationstransfers und die Anordnung und Wachstumsart der Gasatome an der Kristallgrenzfläche, was sich wiederum auf die Kristallwachstumsgeschwindigkeit und die Kristallqualität auswirkt. Daher ist die Entwicklung einer systematischen Temperaturfeldkontrolltechnologie erforderlich. Verglichen mit Si-Materialien liegt der Unterschied bei der SiC-Produktion auch in den Hochtemperaturprozessen, wie z. B. Hochtemperatur-Ionenimplantation, Hochtemperaturoxidation, Hochtemperaturaktivierung und dem für diese Hochtemperaturprozesse erforderlichen Hartmaskenprozess.
Langsames Kristallwachstum: Die Wachstumsrate eines Si-Kristallstabs kann 30 bis 150 mm/h erreichen, und die Produktion eines 1–3 m langen Siliziumkristallstabs dauert nur etwa 1 Tag. Bei einem SiC-Kristallstab mit der PVT-Methode beispielsweise beträgt die Wachstumsrate etwa 0,2–0,4 mm/h, und in 7 Tagen wächst er weniger als 3–6 cm. Die Wachstumsrate beträgt weniger als 1 % des Siliziummaterials, und die Produktionskapazität ist äußerst begrenzt.
Hohe Produktparameter und geringe Ausbeute: Zu den Kernparametern des SiC-Substrats zählen Mikrotubuli-Dichte, Versetzungsdichte, spezifischer Widerstand, Verzug, Oberflächenrauheit usw. Es handelt sich um eine komplexe Systemtechnik, um Atome in einer geschlossenen Hochtemperaturkammer anzuordnen und das Kristallwachstum abzuschließen, während die Parameterindizes kontrolliert werden.
Das Material weist eine hohe Härte, hohe Sprödigkeit, lange Schnittzeiten und einen hohen Verschleiß auf: SiC hat eine Mohs-Härte von 9,25, die nach Diamant die zweithöchste Härte aufweist. Dies erschwert das Schneiden, Schleifen und Polieren erheblich. Das Schneiden von 35–40 Stück eines 3 cm dicken Barrens dauert etwa 120 Stunden. Aufgrund der hohen Sprödigkeit von SiC ist zudem der Verschleiß bei der Waferverarbeitung höher, und die Ausbringungsquote beträgt nur etwa 60 %.
Entwicklungstrend: Größenzunahme + Preissenkung
Der globale SiC-Markt für 6-Zoll-Serienfertigungslinien reift heran, und führende Unternehmen sind in den 8-Zoll-Markt eingestiegen. Inländische Entwicklungsprojekte konzentrieren sich hauptsächlich auf 6 Zoll. Obwohl die meisten inländischen Unternehmen derzeit noch auf 4-Zoll-Produktionslinien setzen, expandiert die Branche schrittweise auf 6 Zoll. Mit der Reife der 6-Zoll-Fertigungstechnologie verbessert sich auch die inländische SiC-Substrattechnologie schrittweise. Die Skaleneffekte der Großserienfertigungslinien werden sich widerspiegeln, und die derzeitige Zeitspanne für die inländische 6-Zoll-Massenproduktion hat sich auf 7 Jahre verringert. Die größere Wafergröße kann die Anzahl der Einzelchips erhöhen, die Ausbeute verbessern und den Anteil der Randchips reduzieren. Die Forschungs- und Entwicklungskosten sowie der Ausbeuteverlust werden bei etwa 7 % gehalten, wodurch die Waferauslastung verbessert wird.
Es gibt noch viele Schwierigkeiten beim Gerätedesign
Die Kommerzialisierung von SiC-Dioden verbessert sich sukzessive. Derzeit haben zahlreiche inländische Hersteller SiC-SBD-Produkte entwickelt. SiC-SBD-Produkte für Mittel- und Hochspannung weisen eine gute Stabilität auf. Im Fahrzeug-OBC wird durch den Einsatz von SiC-SBD+SI-IGBT eine stabile Stromdichte erreicht. Derzeit gibt es in China keine Hindernisse für die Patentierung von SiC-SBD-Produkten, und der Abstand zum Ausland ist gering.
SiC-MOS weist noch immer viele Schwierigkeiten auf. Es besteht noch eine Lücke zwischen SiC-MOS- und ausländischen Herstellern, und die entsprechende Fertigungsplattform befindet sich noch im Aufbau. Derzeit haben ST, Infineon, Rohm und andere 600–1700-V-SiC-MOS die Massenproduktion erreicht und Verträge mit vielen Fertigungsunternehmen unterzeichnet und ausgeliefert. Das aktuelle inländische SiC-MOS-Design ist zwar im Wesentlichen abgeschlossen, eine Reihe von Designherstellern arbeiten jedoch noch mit Fabs in der Wafer-Flow-Phase, und die spätere Kundenüberprüfung benötigt noch einige Zeit, sodass es bis zur großflächigen Kommerzialisierung noch lange dauern wird.
Derzeit ist die planare Struktur die gängige Wahl, und der Grabentyp wird zukünftig im Hochdruckbereich weit verbreitet sein. Es gibt viele Hersteller von SiC-MOS mit planarer Struktur. Im Vergleich zur Rillenstruktur treten bei der planaren Struktur weniger lokale Durchschlagsprobleme auf, die die Stabilität beeinträchtigen. Sie bietet ein breites Anwendungsspektrum im Markt unter 1200 V. Die planare Struktur ist relativ einfach herzustellen und erfüllt die beiden Aspekte Herstellbarkeit und Kostenkontrolle. Rillenbauelemente bieten die Vorteile einer extrem niedrigen parasitären Induktivität, hoher Schaltgeschwindigkeit, geringer Verluste und relativ hoher Leistung.
2 – Neuigkeiten zu SiC-Wafern
Wachstum der Produktion und des Umsatzes auf dem Siliziumkarbidmarkt, achten Sie auf das strukturelle Ungleichgewicht zwischen Angebot und Nachfrage
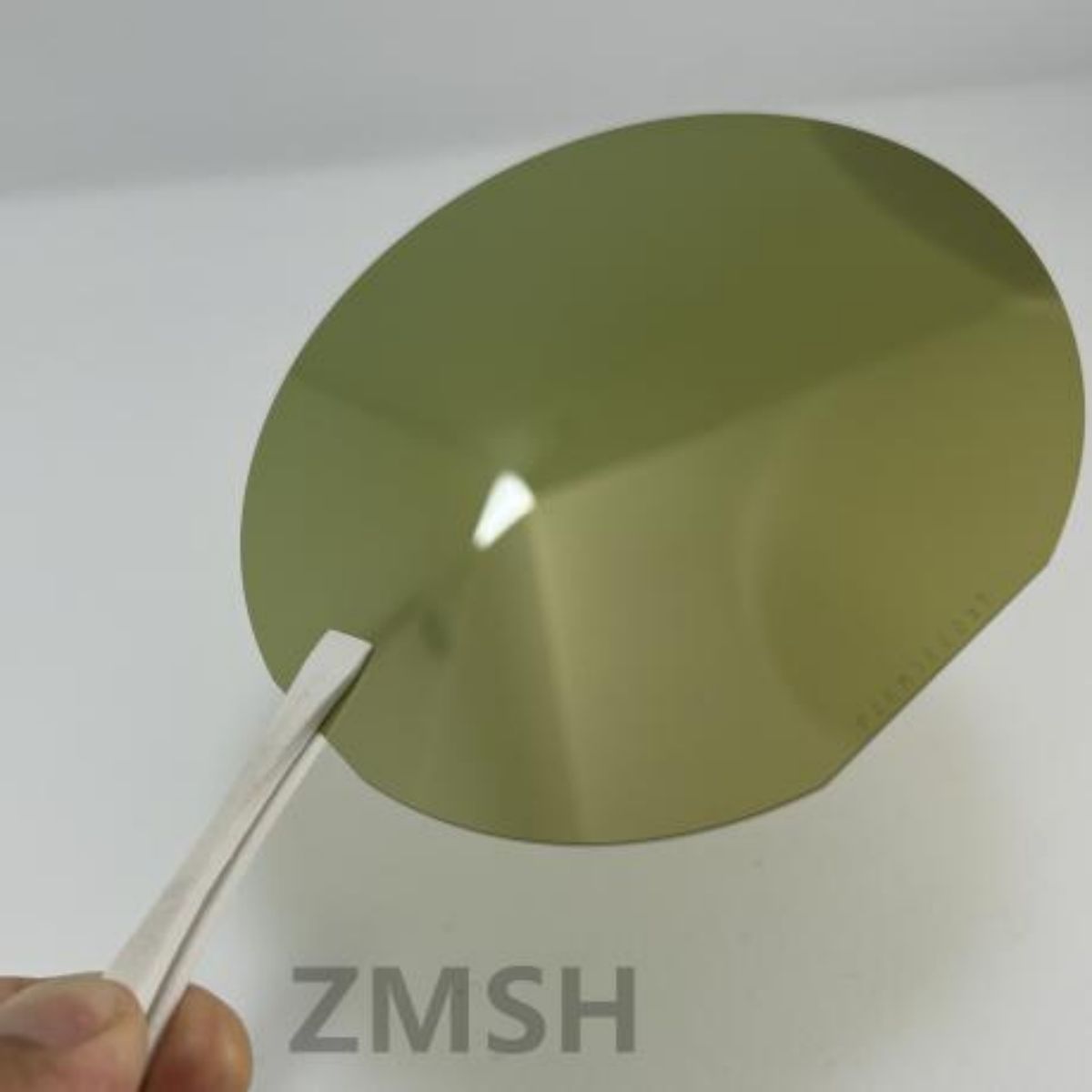
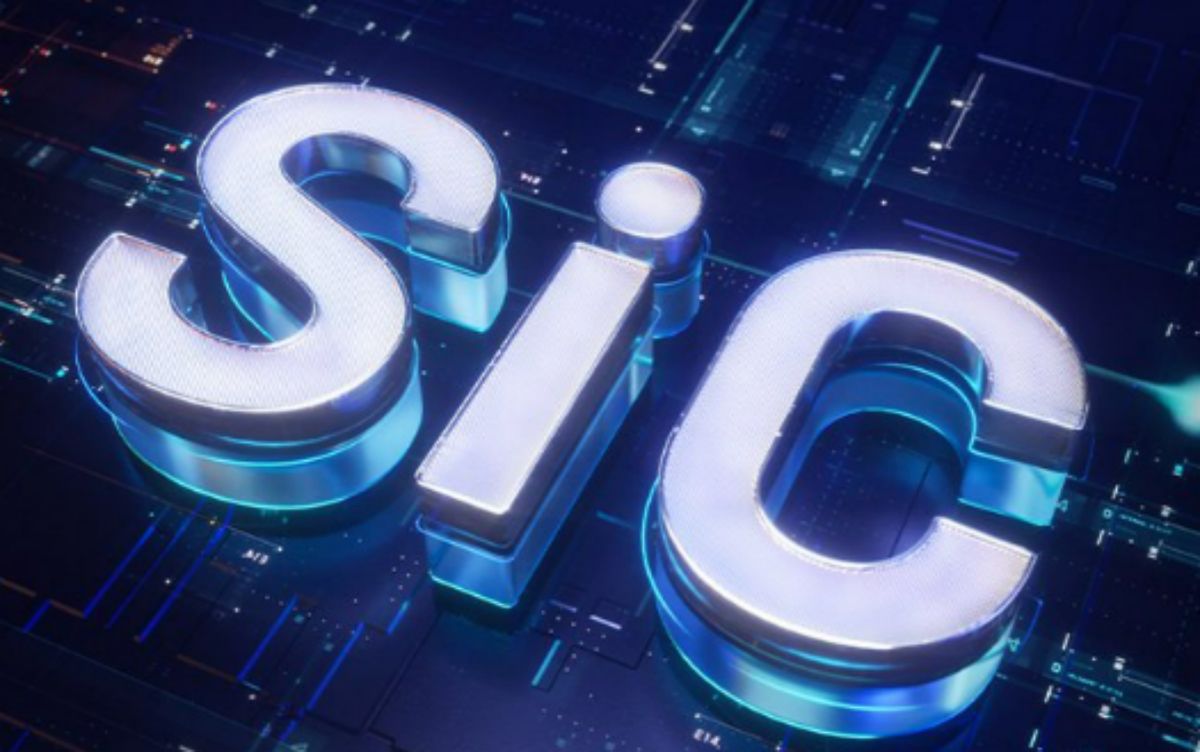
Mit der rasant steigenden Nachfrage nach Hochfrequenz- und Hochleistungselektronik stoßen siliziumbasierte Halbleiterbauelemente zunehmend an ihre physikalischen Grenzen, und Siliziumkarbid (SiC), Halbleitermaterialien der dritten Generation, werden zunehmend industriell eingesetzt. Im Hinblick auf die Materialleistung weist Siliziumkarbid eine dreimal so große Bandlücke auf wie Silizium, eine zehnmal so hohe kritische Durchbruchfeldstärke und eine dreimal so hohe Wärmeleitfähigkeit. Daher eignen sich Siliziumkarbid-Bauelemente für Anwendungen wie Hochfrequenz, Hochdruck, Hochtemperatur und andere Anwendungen und tragen zur Verbesserung der Effizienz und Leistungsdichte leistungselektronischer Systeme bei.
Derzeit sind SiC-Dioden und SiC-MOSFETs allmählich auf den Markt gekommen, und es gibt ausgereiftere Produkte, unter denen SiC-Dioden in einigen Bereichen weit verbreitet sind, anstatt Dioden auf Siliziumbasis, da sie nicht den Vorteil der Sperrverzögerungsladung haben; SiC-MOSFETs werden auch zunehmend in der Automobilindustrie, bei Energiespeichern, Ladesäulen, in der Photovoltaik und anderen Bereichen eingesetzt; im Bereich der Automobilanwendungen wird der Trend zur Modularisierung immer deutlicher, und die überlegene Leistung von SiC muss auf fortschrittliche Verpackungsprozesse angewiesen sein, um zu erreichen, wobei technisch relativ ausgereifte Schalenversiegelungen als Mainstream gelten, die Zukunft oder die Entwicklung von Kunststoffversiegelungen, deren kundenspezifische Entwicklungseigenschaften besser für SiC-Module geeignet sind.
Siliziumkarbid-Preisrückgangsgeschwindigkeit jenseits aller Vorstellungskraft
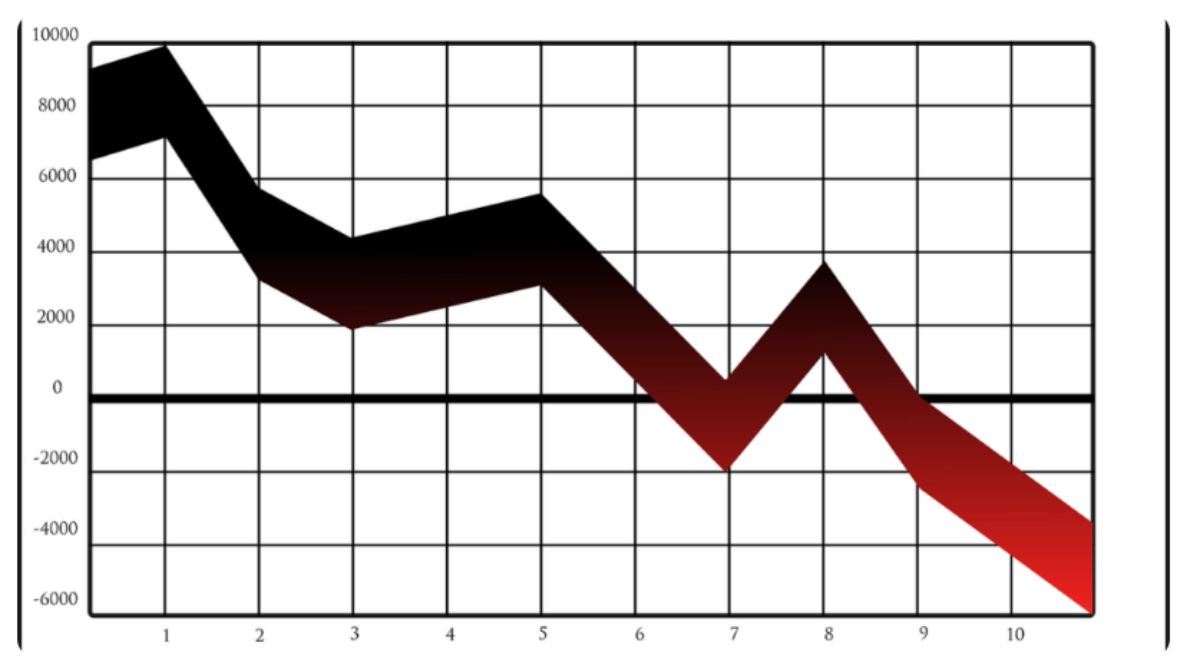
Die Anwendung von Siliziumkarbid-Bauelementen wird hauptsächlich durch die hohen Kosten eingeschränkt. Der Preis eines SiC-MOSFETs auf gleichem Niveau ist viermal höher als der eines Si-basierten IGBT. Dies liegt daran, dass der Siliziumkarbid-Prozess komplex ist. Das Wachstum von Einkristallen und Epitaxie ist nicht nur umweltschädlich, sondern auch langsam, und die Verarbeitung des Einkristalls zum Substrat muss Schneide- und Polierprozesse durchlaufen. Aufgrund der Materialeigenschaften und der unausgereiften Verarbeitungstechnologie liegt die Ausbeute an inländischem Substrat unter 50 %, was verschiedene Faktoren zu hohen Substrat- und Epitaxiepreisen führt.
Die Kostenzusammensetzung von Siliziumkarbid-Bauelementen und siliziumbasierten Bauelementen ist jedoch diametral entgegengesetzt: Die Substrat- und Epitaxiekosten des Frontkanals machen 47 % bzw. 23 % des gesamten Bauelements aus, insgesamt also etwa 70 %, während die Bauelementkonstruktion, -herstellung und -versiegelung des Backkanals nur 30 % ausmachen. Die Produktionskosten siliziumbasierter Bauelemente konzentrieren sich hauptsächlich auf die Waferherstellung des Backkanals (etwa 50 %) und die Substratkosten machen nur 7 % aus. Das Phänomen der verkehrten Wertschöpfungskette der Siliziumkarbid-Industrie bedeutet, dass die vorgelagerten Hersteller von Substratepitaxie das Hauptmitspracherecht haben, was für die Gestaltung in- und ausländischer Unternehmen von entscheidender Bedeutung ist.
Aus dynamischer Sicht auf dem Markt bedeutet eine Kostensenkung bei Siliziumkarbid neben der Verbesserung des Siliziumkarbid-Langkristalls und des Schneideprozesses auch eine Vergrößerung der Wafergröße. Dies ist auch ein ausgereifter Weg in der Halbleiterentwicklung der Vergangenheit. Daten von Wolfspeed zeigen, dass durch eine Vergrößerung des Siliziumkarbid-Substrats von 6 Zoll auf 8 Zoll die Produktion qualifizierter Chips um 80–90 % gesteigert und die Ausbeute verbessert werden kann. Die kombinierten Stückkosten können um 50 % gesenkt werden.
2023 ist als das „erste Jahr des 8-Zoll-SiC“ bekannt. In diesem Jahr beschleunigen in- und ausländische Siliziumkarbidhersteller die Entwicklung von 8-Zoll-Siliziumkarbid. Wolfspeed beispielsweise investiert 14,55 Milliarden US-Dollar in die Ausweitung der Siliziumkarbidproduktion. Ein wichtiger Teil davon ist der Bau einer Fabrik zur Herstellung von 8-Zoll-SiC-Substraten, um die zukünftige Versorgung einer Reihe von Unternehmen mit 200 mm SiC-Bare-Metal sicherzustellen. Die inländischen Unternehmen Tianyue Advanced und Tianke Heda haben außerdem langfristige Verträge mit Infineon über die zukünftige Lieferung von 8-Zoll-Siliziumkarbidsubstraten unterzeichnet.
Ab diesem Jahr wird die Siliziumkarbid-Größe von 6 Zoll auf 8 Zoll anwachsen. Wolfspeed geht davon aus, dass die Stückkosten für 8-Zoll-Substrate bis 2024 im Vergleich zu den Stückkosten für 6-Zoll-Substrate im Jahr 2022 um mehr als 60 % sinken werden. Dieser Kostenrückgang wird den Anwendungsmarkt weiter öffnen, wie aus Forschungsdaten von Ji Bond Consulting hervorgeht. Der aktuelle Marktanteil von 8-Zoll-Produkten liegt bei weniger als 2 %, wird aber bis 2026 voraussichtlich auf etwa 15 % steigen.
Tatsächlich dürfte die Geschwindigkeit des Preisverfalls bei Siliziumkarbidsubstraten die Vorstellungskraft vieler übersteigen. Das aktuelle Marktangebot für 6-Zoll-Substrate liegt bei 4.000 bis 5.000 Yuan/Stück und ist im Vergleich zum Jahresbeginn stark gesunken. Im nächsten Jahr wird ein Preisrückgang unter 4.000 Yuan erwartet. Es ist erwähnenswert, dass einige Hersteller ihre Verkaufspreise unter die Kostengrenze gesenkt haben, um den ersten Markt zu erobern. Dies hat einen Preiskampf ausgelöst, der sich hauptsächlich darauf konzentriert, dass das Angebot an Siliziumkarbidsubstraten im Niederspannungsbereich relativ ausreichend ist. In- und ausländische Hersteller erweitern ihre Produktionskapazitäten aggressiv, oder sie lassen das Überangebot an Siliziumkarbidsubstraten früher als erwartet eintreten.
Veröffentlichungszeit: 19. Januar 2024